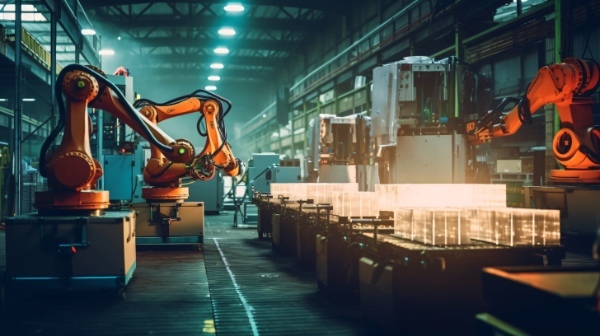
デジタル技術が私たちの生活を大きく変えているように、ものづくりにも大きな変化=「デジタルトランスフォーメーション(DX)」が起きています。製造業におけるDXの代表的な例が「スマートファクトリー」です。スマートファクトリーは、従来の工場にデジタル技術を導入することで、より効率的で高品質なものづくりを実現する新しい工場の形です。
この記事では、スマートファクトリーの概要や導入のメリットについて、具体的な事例を交えながら詳しく解説します。
目次
スマートファクトリーとは?
ここでは、スマートファクトリーについて定義や従来の工場との違いを解説します。あわせて用語として混同されやすいDXとの違いも解説します。
スマートファクトリーの定義
スマートファクトリーとは、デジタル技術の活用によって業務プロセスの改革や生産性・品質の向上を継続的に行う工場のことを指します。
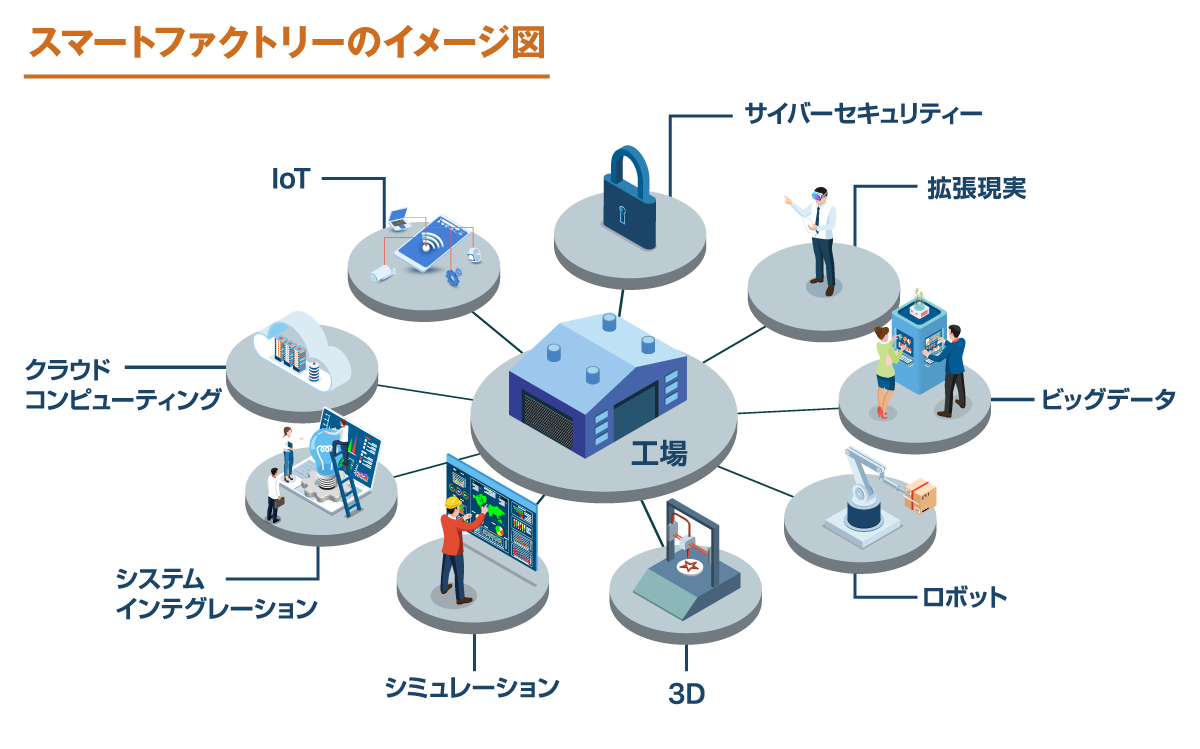
経済産業省の提唱する「ものづくりのスマート化」をもとに、第4次産業革命に対応した新しい形の工場ともいえるでしょう。IoT(モノのインターネット)、ビッグデータ、AI(人工知能)、ロボットなどの先端技術を導入・活用することで、エンジニアリングチェーンやサプライチェーンをネットワーク化、最適化、⾃動化し、製造工程全体の効率化や品質向上を目指しています。
【図】経済産業省による「ものづくりのスマート化」のイメージ
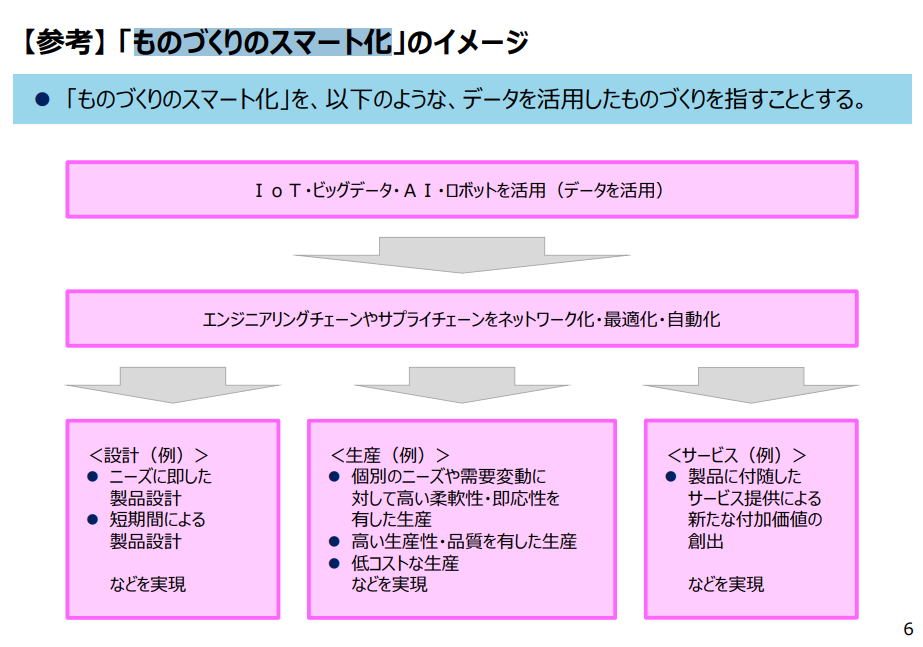
スマートファクトリーを実現するためには、IoTやAI、クラウド、ビッグデータといった先進的なデジタル技術の導入・活用が不可欠です。たとえば、IoTで収集した設備の稼働状況のデータをクラウド上に蓄積し、そこで生まれたビッグデータをAIが分析することで、設備の動作を最適化することができます。
スマートファクトリーは、これらの先端技術「そのもの」ではありません。これらを活用してものづくりの現場を見える化し、ムダをなくし効率を高めて生産性を上げたり、新しい時代に対応した生産現場や企業のあり方を進めたりするものと考えられます。
スマートファクトリーと従来の工場との違い
スマートファクトリーの原型になったのは、2011年にドイツ政府が掲げた「インダストリー4.0」という国家プロジェクトです。「インダストリー4.0」は、IoTやAIといったデジタル技術を積極的に取り入れて製造業を変革することを目指したプロジェクトであり、次の4つの設計原則を定めました。
相互運用性:工場内の人や設備、システムなどが相互につながり、通信を行うこと
情報の透明性:工場内のあらゆるデータを蓄積して見える化し、分析すること
技術的な補助:人にとって危険または困難な課題を設備やシステムがサポートすること
分散型決定:設備やシステムが可能な範囲で自律的に意思決定を行うこと
この4つの設計原則は、スマートファクトリーを理解する上で重要なポイントとなります。
DXとスマートファクトリーの違い
DX(デジタルトランスフォーメーション)とスマートファクトリーは、どちらも「デジタル技術を活用して企業を変革する」という点で共通点がありますが、その範囲や目的が異なります。DXとは、企業がデジタル技術を活用して、ビジネスモデルや業務プロセス、製品やサービスなど企業が提供する価値、そして顧客との関係性までを含むあらゆるものを根本から変革することを指します。
単にITシステムを導入することをDXと呼ぶのではなく「企業全体」の「文化や組織構造まで含めた変革」がなされたとき、DXが導入されたといえるでしょう。
そもそもDX(デジタルトランスフォーメーション)とは何か
・デジタル技術やツールを導入すること自体ではなく、
データやデジタル技術を使って、顧客目線で新たな価値を創出していくこと。
・また、そのためにビジネスモデルや企業文化等の変革に取り組むことが重要となる。
(出典)経済産業省:デジタルガバナンス・コード 実践の手引き(要約版)
関連記事:デジタルガバナンス・コードとは?DX成功に不可欠な最新ガイドラインを解説
一方、スマートファクトリーは前述のとおり、特に「製造業(ものづくりの現場)」においてIoT、AI、ロボットなどのデジタル技術を導入し生産プロセスを最適化することで、「生産性や品質向上を目指す生産体制」の構築を目的とします。
DXが先進技術を用いた企業全体の変革を目的とするのに対し、スマートファクトリーは製造現場に特化した変革です。ここからスマートファクトリーは、DXの取り組みの一部と考えることができます。しかし同時にスマートファクトリーで得られたデータや知見は、企業全体のDXを推進するうえで重要な資産となります。
スマートファクトリーは、これからの製造業が国内外で競争力を維持するために重要な取り組みの一つであり、多くの企業が実現に向けて動き始めています。
スマートファクトリーの8つのメリット
製造業がスマートファクトリーを実現すると、どのようなメリットを得られるのでしょうか。ここでは、主な8つのメリットについて解説します。
【スマートファクトリーの8つのメリット】
【メリット1】生産性の向上
【メリット2】品質向上効果が得られる
【メリット3】コスト削減になる
【メリット4】リードタイムの短縮が可能
【メリット5】技術継承の問題が解決できる
【メリット6】提供価値・イノベーションの創出
【メリット7】人手不足の解消
【メリット8】工場内の導線の再確認と改善
【メリット1】生産性の向上
スマートファクトリーは生産性の向上を実現します。工場内のあらゆる人や設備からIoTでデータを収集し、製造工程全体を「見える化」することで、生産効率を下げる要因を発見して改善しやすくなるためです。
たとえば、工場では設備トラブルによるチョコ停(「チョコっと停止」を短縮した言い方。短時間で復旧可能な製造設備や生産の停止・空転トラブル)やドカ停(「ドカっと停止」を短縮した言い方。長時間の製造設備や生産の停止・空転トラブル)が少なからず発生してしまいます。
設備トラブルは生産性や品質の悪化につながるだけでなく、最悪の場合はラインが停止して大きな損害を招くリスクをはらんでいます。しかし、DXによって設備の動作データをリアルタイムに収集し傾向などを分析することで、トラブル発生をすぐに検知して対処したり、トラブルの予兆を検知して未然に防いだりできるようになります。
【メリット2】品質向上効果が得られる
不良率の低減や品質の安定化は製造業にとって大きな課題です。スマートファクトリーには品質を向上させる効果もあります。
たとえば、人が作業をする様子や設備の動作をリアルタイムに収集・分析すれば、不良が発生しても素早く対処できます。また、蓄積されたデータから不良の原因を特定して改善することで、恒久的な対策を取れるようになります。
【メリット3】コスト削減になる
スマートファクトリーを実現すれば、工場内の設備や人の稼働状況が最適化され、効率的にものづくりを行えるようになります。不良品の発生数が減るため、その分の原材料費が無駄になりません。また廃棄にかかる費用も削減できます。従来に比べて短い時間で生産ができるので、燃料費も抑えられるでしょう。このように、トータルでのコスト削減効果が期待できます。
【メリット4】リードタイムの短縮が可能
スマートファクトリーでは、設計段階から量産に至るまでものづくりのあらゆるデータが蓄積されていきます。これらのデータを活用すれば、新製品の企画から市場投入までのリードタイムを大幅に短縮できます。
たとえば、過去の設計モデルや製造工程のデータを蓄積したレシピを作成しておけば、類似製品を作る際に応用できるでしょう。さらに、デジタル空間上で生産ラインを再現して試作を繰り返すことも可能です。現物である製造ラインを購入・設置して試作や試運転を行う必要がなく、仮想空間でのシミュレーションでスムーズに量産化ができるようになります。必要な配置人員数や製造ラインの効率的な導線などもこの過程で知ることができます。
【メリット5】技術継承の問題が解決できる
スマートファクトリーを取り入れることで、製造業全体の課題となっている技術継承の問題が解決できます。製造業ではベテラン技術者にしかできない作業が多く、属人化が進んでいるケースが多く見られます。そのままだと工場全体の生産性が上がらないだけでなく、ベテラン技術者の高齢化に伴って技術が失われてしまう恐れもあるため、早急な対策が求められます。
スマートファクトリーでは、ベテラン技術者の動きをセンサなどで収集し、分析することで、技術やノウハウをデータ化できます。そのデータを他の技術者への教育に役立てたり、ロボットでの自動化に活用したりすれば、技術継承の課題が解消されます。
【メリット6】提供価値・イノベーションの創出
生産性向上、納期短縮、コスト削減などはそれ自体もメリットですが、削減できたリソースで商品の価値を上げたり、新たなイノベーションを創出したりすることが可能になる点も大きなメリットです。
たとえば、社内の各部門のデータを連携し情報共有することで、生産体制を最適化することができます。どの部門のどの部品が不足しているか、過剰なのかが分かれば修理用の部品供給予測が可能になり、トラブルが起きた際にも迅速に稼働できます。また在庫過多を防ぎ無駄な発注やメンテナンス費用を削減できるでしょう。
他に、新たなイノベーションを生み出すことにもつながります。全体を俯瞰して見られることに加え、DXによる需要予測により、今後どのようなものが流行するか、どのような商品が消費者に求められているかが具体的に予測できます。ここから、個々の顧客ニーズに合わせた製品・サービスの提供が、トレンドの波を逃さず提供できるようになります。
流通した製品は、使用状況をモニタリングデータや、ユーザーに対するアンケートなどをもとに改善点や提供すべきサービスが見つかります。また、新たなニーズの掘り起こしのヒントにもなるでしょう。
【メリット7】人手不足の解消
製造業やものづくりにおける最大の課題である人手不足の解消も、スマートファクトリーによる生産性向上によって可能となります。従来は人の手で行っていた作業をロボットなどで自動化できるようになれば、人件費を大幅に削減できるだけでなく、今後さらに深刻化していく人手不足(技術者不足)の解消にもつながります。
なお、DXによってスマートファクトリー化を進めると、製造業で必要なスキルセットもアップデートする必要があります。最も必要になるのは、スマートファクトリーを維持するためのITスキルを持った人材の採用であることは、経営者と人事担当者は念頭に置いておく必要があります。
【メリット8】工場内の導線の再確認と改善
製造ラインの改善で生産性が改善されることはもちろんですが、スマートファクトリーでは人の動きや荷物の搬入・搬出など製造回りの導線改善にも利用できます。最近ではロボットによる自動搬送機も発達しており、これをスムーズに活用するためにも、工場内の設備配置なども棚卸する必要があります。
スマートファクトリーではこれらも問題点として可視化されるため、これまでは「なんとなく不便だな」「なんだかよく搬送機がぶつかりそうになる気がする」と漠然と感じていた課題も解決できます。
スマートファクトリーを目指す際の問題点
スマートファクトリーは多くのメリットをもたらしますが、いくつかの問題点も存在します。
セキュリティ面のリスク問題
スマートファクトリーはネットワークに接続されたデバイスを使用するため、サイバー攻撃などの脅威にさらされる可能性があります。データ漏洩のリスクにより、生産プロセスや機密情報の安全性が脅かされるおそれがあります。またマルウェア感染が起きると組織のネットワークすべてが機能停止するだけでなく、外部へ意図せず感染拡大させてしまう可能性もあります。
このリスクを低減させるためには、社員・従業員へのIT教育を定期的に行う必要があります。
新規システムの導入と運用・レガシーシステムの置き換えなど技術的な問題
スマートファクトリーでは最新のIT技術が活用されますが、その導入や運用には技術的な課題が伴います。新しいシステムやデバイスの導入、ネットワークの設計や統合、データの管理と解析などが必要です。
さらに、古い体制の工場や企業では、レガシーシステムと呼ばれる固有の古いシステムを現在も使い続けているところが少なくありません。これらの要素を生産体制や稼働状況に支障を与えず、置き換えていくことが求められます。
(参考)経済産業省:「DXレポート ~ITシステム「2025年の崖」克服とDXの本格的な展開~」
従業員のスキル不足の問題
スマートファクトリーの導入には、従業員のスキルと能力の向上が不可欠です。デジタル技術やデータ解析、IoTデバイスの操作など、新たなスキルセットが求められます。しかし、従業員の教育やトレーニングの面での課題や適切な人材の確保が難しい場合があります。
投資費用の問題
スマートファクトリーへの移行には、大規模な投資が必要となります。新しい機器やシステムの導入、インフラの整備、従業員のトレーニングコスト、IT人材の採用に伴う人件費などが発生します。これらの費用は、企業にとって負担が大きい場合があり、導入の障壁となる可能性があります。
これらの問題に対処するためには、セキュリティ対策の強化、従業員の教育とトレーニング、IT人材の速やかな確保、将来を見越した資金計画などが重要です。詳しくは後述します。
スマートファクトリーを実現するための4ステップ
これから自社のスマートファクトリー化を進めていこうと考えたときに、何から取り組んだらよいのかが分からないという方は多いでしょう。経済産業省は「スマートファクトリーロードマップ」の中で、企業がスマートファクトリー化を進める手順を示しています。ここでは、経済産業省の示す手順を参考に、どのようにスマートファクトリー化を進めていけばよいかを解説します。

1.目的・目標を定める
まずは、自社の課題や戦略を踏まえてスマートファクトリー化の目的・目標を定めましょう。最初のうちは、あれこれと手を出すのではなく、目的・目標をある程度絞ってスマートファクトリー化を進めていくと失敗しにくくなります。
2.データの収集・蓄積
目的・目標を達成するために「どのようなデータが必要になるか」「どこからそのデータを集められるか」を特定します。その上で、IoT技術を導入して実際にデータを収集・蓄積していきます。
3.データによる分析・予測
収集・蓄積したデータを分析して、目的・目標を達成するために役立つ要素を抽出します。たとえば、工場の生産性向上を目的とする場合は、生産効率を下げる要因になっている設備や人、工程を見つけていきます。これを繰り返していくと、事象がパターン化されて将来予測ができるようになります。
4.データによる制御・最適化
分析・予測した結果をもとに、設備を制御したり、人の作業手順や生産計画を最適化したりします。まずは、データをもとにして人の手で制御・最適化を行いますが、最終的にはAIを活用して設備やシステムが自律的に意思決定を行うことを目指していきます。
スマートファクトリー化を進める上での3つのポイント
上述した「スマートファクトリーロードマップ」の中には、スマートファクトリー化を進める上でのポイントも示されています。そちらを参考に、製造業がスマートファクトリー化を成功させるために重要なポイントを3つご紹介します。
スモールスタートで改善を繰り返す
スマートファクトリー化を進めるにあたって、いきなり大規模にシステムを刷新しようとしたり、すべての設備のIoT化に取り組んだりすると、失敗しやすくなります。スマートファクトリー化の鉄則はスモールスタートであり、まずは成果の出やすい特定の業務や工程、設備に絞って取り組んでいくのがおすすめです。
この理由として、スマートファクトリー化は、既存の工場のあり方や業務内容を大きく変革する取り組みのため、進める過程で従業員に少なからず負担がかかることが挙げられます。成果を急ぎ早急すぎる導入を行うと、新しいやり方になじめない従業員が大量に発生し、かえって業務が遅滞してしまったり、最悪、元の古いシステムに戻さざるを得ない事態になったりというリスクがあります。
まずは自社の課題や戦略を明確にし、特に課題の大きい部分からスマートファクトリー化を進めるようにしましょう。短いサイクルでPDCA(Plan・Do・Check・Action)を繰り返してノウハウを蓄積しつつ、徐々に対象範囲を拡大していくのが、スマートファクトリーを実現するための近道です。
なおシステムやソフトウェアを開発する場合に使われる、小さな単位で実装とテストを繰り返すアジャイル開発・スクラム開発がスマートファクトリー化にも適しています。
企業全体が目指す姿を共有し、「全体最適」を意識する
スマートファクトリー化は全社的な取り組みであるため、あらゆる部門や担当者が関わることになります。各部門や担当者の立場ではついつい、その部門のみが改善されればよいと「部分最適」を目指しがちですが、あくまでも組織全体が改善・最適化される「全体最適」を意識しながら進めなければなりません。
スマートファクトリー化を進める際は、初期の段階から関係部門のメンバーが集まり、企業として目指す姿の共通認識を図りながら推進する体制を構築しましょう。また、経営者自身が強い意思を持ち、スマートファクトリー化を主導する姿勢も重要です。
取り組みの成果を定期的にモニタリングする
前述のとおり、スマートファクトリー化は既存の工場のあり方や業務内容を大きく変革する取り組みのため、従業員に負担がかかります。新しい仕組みに従業員にも馴染んでもらわなければならないのですが、モチベーションを維持するのが難しいという課題があります。
従業員のモチベーションを維持するためには、スマートファクトリー化によってどういった効果を得られたのか、どれだけ業務が楽になったのか、といった成果を定期的に共有することが重要です。成果を実感して手応えを得ることで、スマートファクトリーの実現に向けた取り組みが定着しやすくなります。そういった観点からも、スモールスタートによって短いサイクルで成果を実感していくのが効果的といえるでしょう。
【関連記事】
アジャイル開発とは? スクラム開発の違いとそれぞれのメリットを解説
スマートファクトリーの事例3選
すでにさまざまな企業がスマートファクトリー化に取り組み、一定の成果を上げています。ここでは、スマートファクトリーの参考事例として3社の取り組みをご紹介します。
生産性の向上を実現した事例
ある工作機械メーカーでは、グローバルな市場で販売数を増やすためには工場の生産性を極限まで高める必要があると考え、1日24時間・週7日稼働する工場を目指しました。
たとえば、IoTを活用して生産の進捗状況と設備の稼働状況を同時に監視・見える化するシステムを導入し、稼働状況をフロアマップやグラフで表示することで、稼働の最適化を図っています。また、生産途中の製品すべてにIDをつけて管理することで位置や状態を把握し、最適なスケジュールでの生産を実現しています。
品質の向上を実現した事例
ある化学品メーカーでは、品質改善・生産性向上を実現するために画像解析システムを実用化しました。複数のカメラを用いて作業者(Man)・設備(Machine)・材料(Material)の3Mの状態を撮影し、撮影した映像を解析することで、作業員のミスや不具合の予兆を発見するという仕組みです。
また、映像データを蓄積して正常なデータと連携することで、不具合発生時の原因究明のスピードアップや、改善すべき箇所の解析を可能にしています。
技術継承の課題を解決した事例
ある空調メーカーでは、グローバル化にあたって課題となった技術者不足を解消するために、スマートファクトリー化を推進しています。
たとえば、空調機の生産でカギを握る技能とノウハウをデータ化するために、IoTや画像解析技術を活用して熟練技術者の動きや状態を計測・解析を実施しました。得られたデータをもとに技能習得の支援システムを構築することで、習得にかかる期間を約2分の1に短縮できたといいます。
まとめ
この記事ではスマートファクトリーについて解説しました。スマートファクトリー化によって生産効率が上がりコスト削減になるほか、従来の工場は難しかった人手不足や技術継承など、さまざまな課題が解決できるメリットがあります。ただし導入の際には、一斉にシステムの入れ替えなどを行うのでなく、従業員のモチベーション維持に配慮しながらスモールスタートすることが重要です。
多くの企業がスマートファクトリーの実現に向けた取り組みを進めていますが、実はノウハウのない企業にとっては容易なことではありません。IT人材の確保も昨今は難しく、レガシーシステムに慣れた高齢の従業員などに新しい仕組みになじんでもらうには、相応のプロセスが必要になります。
まずは、自社の製造工程の中でも特に重要な部分に注目して課題を整理し、データ収集・蓄積をすることから始めてみてはいかがでしょうか。
【注目コンテンツ】
・DX・ESGの具体的な取り組みを紹介!専門家インタビュー
・DX人材は社内にあり!リコーに学ぶ技術者リスキリングの重要性
・サービタイゼーションによる付加価値の創造と競争力の強化