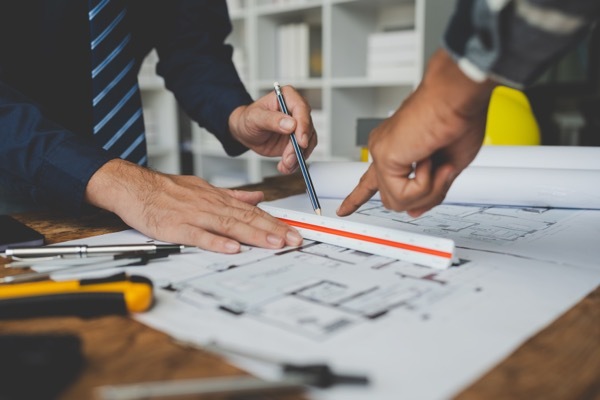
DRBFMとは、トヨタグループが2001年から試行している新規問題の未然防止手法です。部門を超えた専門家が変更点や変化点に着目して議論することで、問題を未然に防ぎます。DRBFMを効果的に実施するには、どのような手順を踏みながら議論すればよいのでしょうか。
DRBFMとは
DRBFM(Design Review Based on Failure Mode)とは、トヨタグループが2001年から試行しているレビュー方法で、その名の通り故障モード(Failure Mode)を基に、DR(Design Review)を行います。DRは「設計審査」と言われることもありますが、DRBFMにおけるDRは「設計の考察・議論」と捉えた方が正しいかもしれません。
以下の図は、トヨタが公表しているDRBFMの概要です。
Step4には「関係者と徹底してDR」という説明と、複数人で議論している様子が示されています。このことからDRBFMにおけるDRは、単なる「審査」ではなく、設計や技術、品質管理などの関係者が徹底的に「議論」するフェーズだと捉えることができます。
DRでは、変更点と変化点に着目して心配点を導き出し、起こり得る問題への対策を講じます。開発段階で問題点を発見して対策を講じることにより、トラブルを未然に防ぐことが可能です。
変更点は意図して設計や仕様を変えた点で、変化点は使用する環境が変わった点を指します。DRBFMでは以前から変化した点に着目して問題点を導き出すため、まずはどこが変わったかを明確にしなければなりません。
また、DRBFMでは変更点や変化点を一覧化したワークシートが用いられます。ワークシートを作成することで、設計や変更点を整理できることに加え、共有が容易になります。事前に要点を整理することにより議論を活発に行えるため、DRBFMにワークシートは欠かせません。
FMEAとは
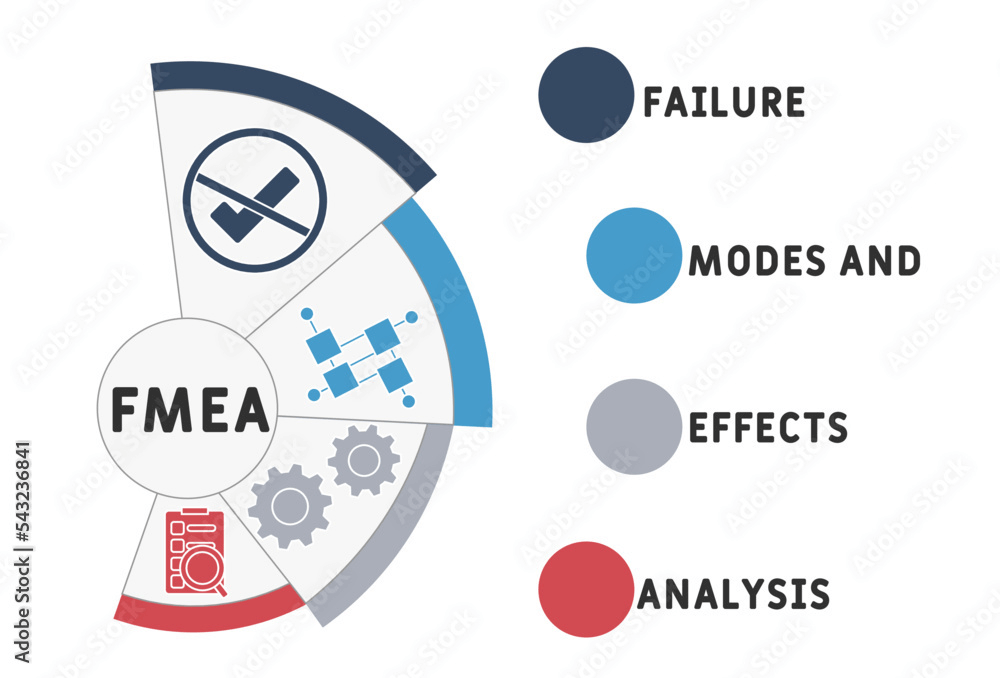
DRBFMと混同される用語にFMEA(Failure Mode and Effects Analysis)があります。FMEAは、事前に予測される故障モードの中から、重要度が高いものを抽出し、対策を講じる手法です。自動車や航空機メーカーなどの企業で、潜在的な故障や不良モードを未然に防ぐために広く利用されています。
FMEAは、重要度の高い故障モードに集中して対策を講じられるというメリットがあります。重要度を明確にせず、すぐにできる対策や簡単な対策から始めると、得られる効果が小さくなってしまう場合がありますが、効果の大きな対策から始めることで、成果を出しやすくなるでしょう。
FMEAでは、重要度の大きさを以下のように求めます。
重要度=発生頻度×影響度×検知難易度
発生頻度とは、不良が発生する頻度のことです。発生頻度が高いほど製品の不良率は上がるため、重要度が高くなります。
影響度とは、不良が起きたときの損失の大きさのことです。例えば、不良が発生した場合でも、製品の利用に問題が生じない場合もあります。この場合、影響度は低いと判断できます。しかし、不良が発生したときに重大な事故が起こる場合は、影響度が高くなります。
検知難易度は、不良品を取り除く難易度のことです。不良があった場合でも、現場で容易に取り除くことができれば顧客に不良品が渡る可能性を低減できます。しかし、検知が難しい場合は不良品が顧客に渡る可能性が高くなるため、注意が必要です。
FMEAでは、以上のように重要度を求め、重要度の高いものから対策を講じます。企業や業界によって重要な要素に加重をかけて計算をすれば、自社に合わせた重要度を知ることが可能です。
DRBFMの目的は問題の未然防止と設計ノウハウの蓄積
ここまでDRBFMとFMEAについてそれぞれ解説してきましたが、これらの違いは目的にあります。DRBFMの目的は「変更点」や「変化点」に着目し、変更によって発生する問題を未然に防ぐことです。一方、FMEAの目的は製品やプロセス全体で発生する問題を未然に防ぐことです。
扱う範囲はFMEAの方が広いため、DRBFMよりも有効と思われるかもしれません。しかし、それぞれにメリットがあるため、場面によって使い分ける必要があります。
例えば、業務内容に変更はなく、業務改善のみを図りたい場合はFMEAが適しています。問題の重要度を定量化できるため、どの問題から取り組めばよいのかを明確にできるでしょう。DRBFMは変更点や変化点の見える化から始めるため、単なる業務改善に役立てることはできません。
DRBFMに向いている場面は、製品をリメイクするときや、新規商品の開発で既存部品を改良するときなどが挙げられます。設計段階でさまざまな視点から議論できるため、検討漏れを防げます。また、議論を重ねることで設計ノウハウが蓄積し、後の商品開発の精度を高めることができるかもしれません。
DRBFMのワークシートの項目
先述の通り、DRBFMを実施する際はワークシートを使うのが効果的です。ワークシートを活用することで、設計や変更点を整理でき、取り組むべき課題が明確になります。DRBFMのワークシートに必要な項目は、大きく分けて以下の7つです。
1. 変更点(変化点)とその目的
2. 変更に関わる心配点
3. 心配点が起こり得るケース
4. 顧客への影響
5. 心配点を除くための設計
6. 推奨する対応
7. 対応の結果
変更点(変化点)とその目的
まず、変化した部分を記載します。例えば「〇〇の素材」「〇〇の幅」などと記載します。また、なぜ変更することになったのか、その目的も記載しましょう。
変更に関わる心配点
考えられる「故障モード」を記載します。具体的には、設計を変更したことにより障害を引き起こす可能性のある機能や、欠如してしまう商品性を記載します。議論により新たな問題が見つかる可能性もあるため、たとえ重要度が低いと考えられる場合でも、思いついた心配点は全て記載するようにしましょう。
心配点が起こり得るケース
どのような場面で「変更に関わる心配点」で記載した故障モードが考えられるかを記載します。物流や販売部門などの設計に詳しくない方が見ても理解できるよう、部位や現象を具体的に記載すると議論をスムーズに進められるでしょう。
顧客への影響
故障モードが顧客に与える影響を記載します。重要度を正確に求めるためにも、考えられる影響を具体的に記載するとよいでしょう。また、考えられる影響が複数ある場合は、漏れなく記載します。影響の程度により、重要度を定めるのも効果的です。
心配点を除くための設計
心配点を除くために、どのような設計をしたのかを記載します。それによって心配点を除くことができているかを第三者が見てもわかるように、可能な限り具体的に記載しましょう。
推奨する対応
DRBFMにより見つかった問題点を記載します。DRBFMでは、問題点を見つけるだけでなく、誰がいつまでに改善するのかまで決定します。ワークシートには担当者や期限も記載しましょう。
対応の結果
「心配点を除くための設計」をすることにより、「変更に関わる心配点」に記載した故障モードがどのくらい解決したかを評価します。この段階で試作やデジタルツインのシミュレーションを実施していれば、その結果も記載しましょう。
DRBFMのやり方と手順
DRBFMを効率的に進めるには、適切な手順を踏むことが重要です。非効率な順番でDRBFMを進めてしまうと、参加メンバーの時間を無駄にしてしまいます。ここでは、適切な手順と効果的なDRBFMの進め方を解説します。
ワークシートへの記載
まず、先ほど解説したDRBFMのワークシートを作成します。
DRBFMでは、変更点(変化点)から問題点を導き出し、防止策を図ります。この部分を見落としてしまうと対策を講じることができなくなってしまうため、漏れなく記載するようにしましょう。
なお、「推奨する対応」はDRBFMで出た問題点を記載する項目のため、設計者が埋める必要はありません。
ワークシートは企業が抱えている問題点に応じて変更することもできます。自社独自のワークシートを作る際は「DRBFMのワークシートの項目」で解説した7つの項目が入っているかを確認しましょう。
DR(デザインレビュー)の開始
設計者によるワークシートへの記入が完了すれば、DRBFMの最も重要な段階であるDRを始めます。設計者が見落としている問題点はないか、さまざまな視点から確認しましょう。
DRは「設計審査」と訳されることがありますが、DRBFMでは「審査」よりも「議論」が重要です。設計者の視点では適切な対策を取っていたとしても、マーケティング視点から見るとより良い対策がある可能性もあります。これは、部門ごとの専門家が集まらないと議論できません。
「この設計で心配点を解消できるか」を審査するだけでなく、「さらに良い設計はないか」を議論することで、あらゆる視点から見て良い製品にすることができます。
DRBFMのポイント
DRBFMを実施する際には、以下のポイントに注意することで、効果を高められます。
・正確にリスクを評価する
・全員で評価する
正確にリスクを評価する
DRBFMの実施にあたっては、正しいリスク評価が重要です。ワークシートの項目だと「変更に関わる心配点」「心配点が起こり得るケース」「顧客への影響」が挙げられます。これらのリスク評価を誤ると、不良品を顧客に提供してしまうリスクが高まります。より良い製品を顧客に届けるために、勘や経験に頼らず、利用できるデータがあれば積極的に活用しましょう。
また、リスクの見落としがあると十分な対策を講じられません。見落としをゼロに近づけるためには、設計者がまとまった時間を取って考えたり、変更点に見落としがないかをダブルチェックしたりするなどの工夫が必要です。リスク評価に専門的な知識が必要な場合は、専門家や関連部門に相談するとよいでしょう。
全員で評価する
多角的な視点から問題点を抽出するためには、部門ごとの有識者が話し合いに加わる必要があります。問題点の見落としを防ぎ、製品のリスクを最小限にするためにも、全員で議論や評価を行いましょう。
全員とは、「設計」に加え「製造」「技術」「品質管理」「検査」「物流」「販売」などに関わる担当者が挙げられます。一部の工程を外注している場合は、外部の人にも議論に参加してもらった方がよいかもしれません。
設計段階からさまざまな部門を巻き込んで議論することで、設計者だけでは気がつかなかった問題点を発見できます。また、設計の段階で製品を作り込むことで、後工程で修正が発生するリスクを低減できます。
DRBFMは議論が最も重要
DRBFMで重要な点は、設計を「審査」するのではなく、「議論」を徹底的に行うことです。さまざまな分野の専門家や有識者が議論を重ねることで、商品を設計の段階で作り込むことができ、修正や見直しの手間が省けるようになるでしょう。
商品の品質やコストの8割は、設計段階で決まると言われています。裏を返せば、高品質で低コストの商品を作るためには、設計段階に注力する必要があるのです。
DRBFMを実施すれば、設計段階での負担は増加しますが、後工程で発生する問題を減らしながら高品質な製品を作れるようになります。設計段階に改善の余地があると感じる場合はDRBFMの考え方を取り入れ、開発工程を見直してみてはいかがでしょうか。
【こんな記事も読まれています】
・【会員限定動画】サプライウェブで実現するマスカスタマイゼーション時代の企業戦略
・製造業における購買・調達業務とは?課題の解決方法も紹介
・ビジネスや技術のトレンドに反応しながら進化を続けるCRMの事例を紹介