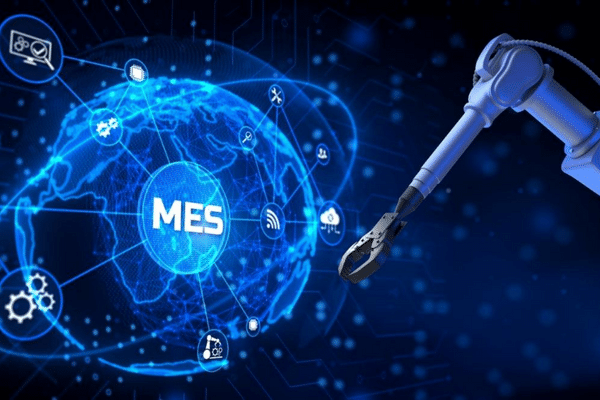
デジタル化が進む現代は、工場でもコンピュータを活用したモノづくりの効率化(DX)が求められています。この流れの中で特に注目されているのが「MES」というシステムです。MESは、工場の生産データをリアルタイムで収集・分析し、製品の不良品発生を早期に検知して原因究明を迅速に行うなど、生産計画の最適化や品質向上に役立てることが可能です。
この記事では、MESの必要とされる背景、具体的な機能や導入のメリット、ERPとの違いについて、わかりやすく解説します。
目次
MES(Manufacturing Execution System)とは?
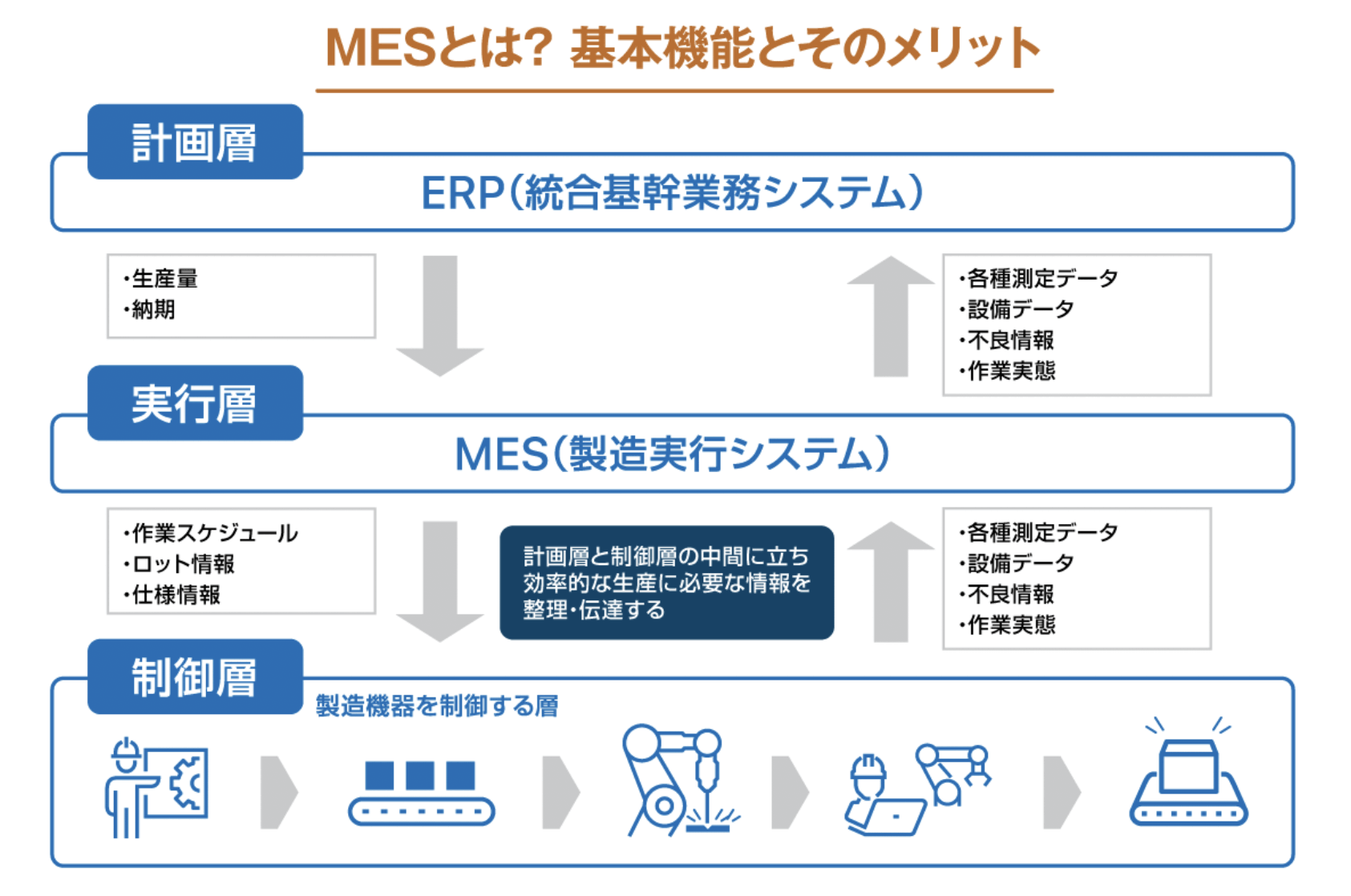
はじめにMESについて「概要と目的」「基本機能と業務範囲」「MESの役割」「ERPとの違い」「種類(オンプレミスとクラウド)」に分け、それぞれ解説します。
MES(Manufacturing Execution System)とは|概要と目的
MES(読み方:エムイーエス)とは「製造実行システム(Manufacturing Execution System)」の略称です。主に製造業で利用されるITシステムの一つで、製造に関わるオペレーションやマネジメント業務をデジタル化し、より効率的かつ正確に作業が行われるよう製造現場の管理や見える化、製造指示、作業者の支援などを行うためのシステムです。
「製造管理システム」「工程管理システム」と呼ぶほうが、実態に近くわかりやすいかもしれません。MESを導入する目的は、生産工程全体を効率化させ、品質向上や設備故障などのリスクを事前予測できるようにすることにあります。
MESを導入することで、製品の仕様・品質を損なうことなく、不良率を低減させて生産効率を高め、QCD(Quality:品質、Cost:コスト、Delivery:納期)の継続的改善が実現します。MESは、これまでの日本の製造業を支えてきた重要なシステムですが、近年は新たな役割を求められるようになっています。
MESの基本機能と業務範囲
MESは、工場の生産ラインの各製造工程と連携し、作業者へ指示を出す役割を担っています。そのため工場の各設備や材料や加工工程などに関する情報をリアルタイムに把握することが可能です。
さらに、ERP(後述)など「計画層」である上位システムから生産量、納期などに関する指示を受けて、作業のスケジューリングを策定し、現場の各ラインにいる作業者に指示を出します。またこの際、ロット情報、仕様情報といった生産に必要な基本情報も「制御層」と呼ばれる工作機械などを稼働させるシステムに伝えるという流れです。
さらにMESは、各種測定データ、設備データ、不良情報、作業実態といった「製品をいくつ・どのようにつくったのか」という情報を、製造ラインを動かしている制御機器およびシステムから受け取り、ERP(統合基幹業務システム)などの上位システムに伝達します。
このようにMESシステムは、ERPなどの計画層と、実際に製造機器を制御する層(上図における制御層)との中間に立ち、効率的な生産に必要な情報を整理、伝達する役割を担っています。
制作現場における情報管理システムの3つの階層とMESの役割
MESの役割を理解するために、製造現場における情報管理を3つの階層に分けて考えてみましょう。
【図】製造現場における情報管理システムの3つの階層
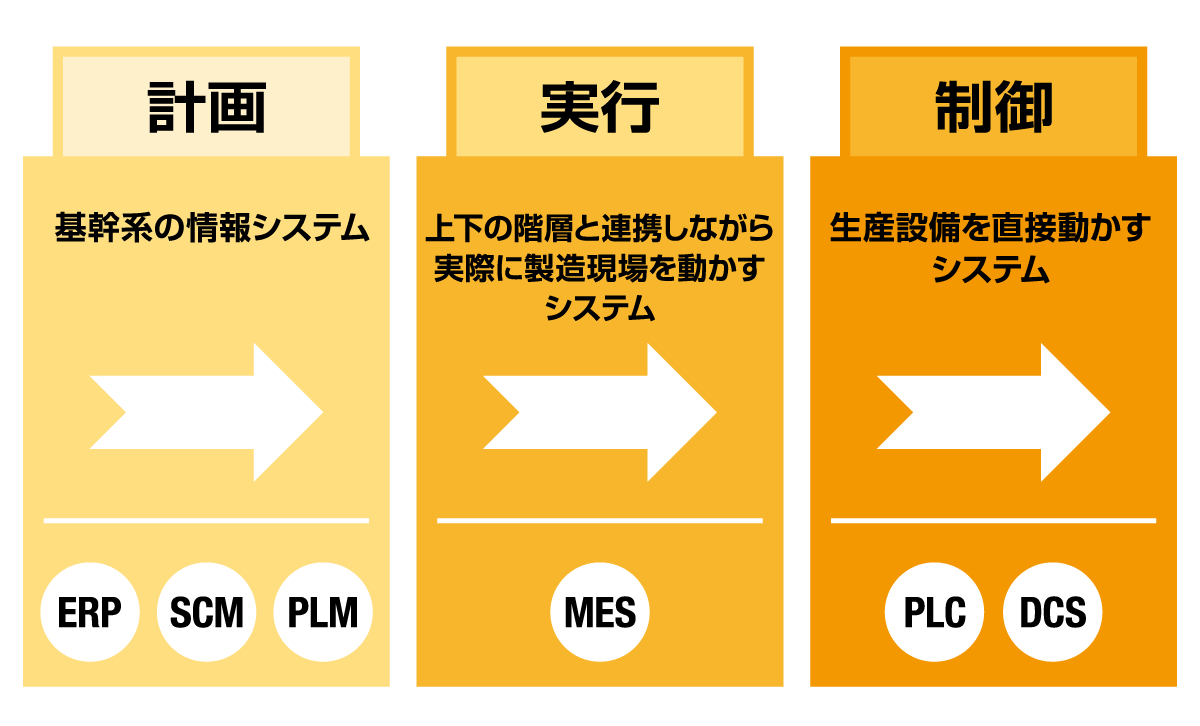
- 計画層:ERP、SCM、PLM、生産管理システムなど基幹系の情報システム(全体的、統合的な管理を行う上位層)
- 実行層:MESなど上下の階層と連携しながら実際に製造現場に指示を出し動かすシステム
- 制御層:PLCやDCS(分散制御システム)など生産設備を直接動かすシステム
一般的に製造業では、全体的な生産計画を計画層にあたる基幹系システムが担っており、その計画にもとづいて製造現場がものづくりを進めていきます。なぜMESのような実行層が必要なのでしょうか。これは、実際にものづくりを行うために製造現場の状況に合わせてより詳細なスケジュールを立てたり、進捗状況をリアルタイムに把握したりする仕組みが必要になるからです。
基幹系システムが立てた生産計画は、粒度が粗いケースが多いため、分単位や秒単位で動くこともある製造現場を管理することには適していません。また基幹系システムの多くは、生産設備との連携機能が充実していないため、リアルタイムな進捗状況を把握するのは困難です。
しかし、より製造現場に近いシステムであるMESを活用すれば、現場から求められるレベルの詳細なスケジュールを立てて作業者や設備へ製造指示を出すことができます。さらにMESは、生産設備との連携機能が強化されているため、各設備からのデータ収集もしやすくなるのです。
MESが実行層として間に入ることによって、製造現場はより一層効率的にものづくりを進められるようになります。またMESに蓄積されたデータを分析すれば、さらなる生産効率の改善に取り組むことも可能です。
MESとERPの違い
【表】MESとERPとの違い
MES | ERP | |
---|---|---|
役割 | 製造業における生産管理や工程管理を担う | あらゆる業界における基幹業務を管理し経営効率化を担う |
日本語訳・呼ばれ方 | ・製造実行システム ・製造管理システム ・工程管理システム など | ・統合基幹業務システム ・基幹システム |
支援対象 | 実行層:製造(実行)工程 | 計画層:計画・準備工程 |
製造業で使われる際の具体的な作業 | 計画層と制御層への情報取次ぎ、製造工程など作業スケジュール・手順の管理と指示 | 生産計画を立てて準備を行う |
使われる業界 | 主に製造業 | さまざまな業界 |
主な活用者 | 生産管理に関わる担当者 | 経営層、基幹業務管理者 |
ERP(Enterprise Resource Planning:企業資源計画)とは、経営や「企業全体」を統合的に管理するシステムで、日本語では「統合基幹業務システム」「基幹システム」と呼ばれます。ERPは、企業の基幹となる「会計」「人事」「生産」「物流」「販売」などの業務を統合し、それらの情報の一元化と統合化を図るシステムです。そのため製造業に限らず、さまざまな業界で活用されています。
一方、MESはより「現場」に近く、工場での各工程における生産性を上げ、スムーズに管理することに特化している点がERPとは異なります。MESで製造工程でのデータをリアルタイムで把握し、ERPに接続することで、スピーディかつ迅速な経営判断につなげることが可能になります。
【関連記事】
MESとERPの違いとは?製造業DXで求められるシステム環境
MESの種類(オンプレミスとクラウド)
MESには、大きく分けてオンプレミス型とクラウド型、2つの種類があります。
・オンプレミス型MESのメリット・デメリット
オンプレミス型MESは、企業内のデータセンターやサーバーにシステムを構築・運用する形態です。企業は独自のハードウェアとソフトウェアインフラストラクチャを所有し、データの保存と処理を自社で管理します。
オンプレミス型MESは、セキュリティやデータの管理に関して企業が完全な制御権限を持つというメリットがあります。また、企業固有の要件や規制などに合わせてカスタマイズすることが比較的容易です。
一方、デメリットとして、以下が懸念されます。
- システムの導入や保守にかかる初期費用がクラウド型よりも高額になる傾向がある
- システムの保全や継続的な運用と改善に投資費用がかかる
- 専門知識のあるIT人材採用が必須
- 拡張性や柔軟性に限界がある
・クラウド型MESのメリット・デメリット
クラウド型MESは、クラウドベースで利用する形態です。ベンダー(クラウドサービスの提供者)が所有するサーバー上でシステムを利用します。収集データやアプリケーションはクラウド上に保存され、インターネットを介してアクセスすることになります。
クラウド型MESのメリットは、インフラストラクチャやアプリケーションの管理をアウトソーシングするため、企業はハードウェアやソフトウェアの購入、保守にかかる負担を軽減できることです。また、クラウド型は柔軟性(※)が高く、リアルタイムのデータ共有が可能であり、複数の拠点やパートナーとの連携が容易です。
※柔軟性:たとえばシステムリソースの増減が容易にできる、サブスクリプション契約のためコストの増減がコントロールしやすいなど
デメリットとしては、データセキュリティやプライバシーに関する懸念があることがリスクになる点が挙げられます。そのほか、インターネット接続に依存するため、通信状況によっては安定した利用が難しくなるおそれがあります。そのためクラウドベースの場合は、ネットワークにおける安定性の確保が極めて重要です。
オンプレミス型MESとクラウド型MESは、どちらが正解というわけではありません。企業は、自社の環境やリソース、コストにフィットしたものをニーズや要件に応じて選択することが必要です。たとえばセキュリティと制御の重要性を重視する場合はオンプレミス型が適しています。
一方、柔軟性とコスト効率を求める場合はクラウド型が選択される傾向があります。企業の戦略と現在のITインフラの状況に合わせて検討されるべきといえるでしょう。
MESの活用事例
MESは、すでにさまざまな業界で活用されています。たとえば航空機向け部品を製造しているある企業では、新たな生産拠点での工程管理や見える化を実施するためにMESを導入しました。工場内の生産設備の情報をIoTで収集し、既存の基幹システムとも連携を行うことで、製造現場で必要な情報をMESに集約。その結果、次のような導入効果を得ることができました。
- 設備停止などのトラブルをシステム上にリアルタイムに表示することで、早期発見・復旧ができるようになった
- 生産の進捗状況をリアルタイムに表示し、進捗の遅れに対して対策を行うことで、効率的なモノづくりが実現した
- 収集した生産実績データを分析することで、品質向上や生産工程の改善を実施できるようになった
・MESがないとどうなる?MESが導入されている・されていない生産現場の違い
逆説的にMESが導入されていない場合、生産現場でどのような問題が起きるかを考えてみましょう。
MESが導入されていない生産現場では……
MESが導入されていない現場では、手書きの指示書や日報、検査記録を運用することになります。また仕様変更、仕掛品の管理などの情報もホワイトボードなどで始業前、作業再開前に確認、共有することがほとんどです。
これでは人為的なミスが発生しやすくなり、スムーズな作業進捗もままならなくなるでしょう。また紙の指示書などは管理する手間もかかり、過去の記録を容易に検索することも難しいです。さらに、MESを導入していない場合、ERPへの実績入力も手動となるため、効率が悪くミスも発生しやすくなります。
また、設備機器のデータをMESによって継続的に管理できていないと、不良品や製造ライン停止の原因究明に時間がかかることも多く、紙の書類で整理されている過去の実績データから調べるしかなくなり、これも大きなロスを生み出すことになりかねません。
このようにMESが導入されていない場合の「最悪の状況」は、生産現場ではいつ起きてもおかしくありません。現状は、そうした事態を起こさないように数多くの現場でさまざまな人の知見、経験によって防いでいるに過ぎません。
MESが導入、活用されている生産現場では……
MESが導入されていない場合に起こりうる問題を防ぐには、あらゆる電子化が不可欠です。つまりMESの導入は、製造業のDX(デジタルトランスフォーメーション)といえるでしょう。
産業界の大きなムーブメントとなっているDXには、さまざまな取り組みが考えられます。特に製造業のDXにおいては、工場など生産現場のDXは避けては通れないテーマです。そして、この取り組みはMESなしでは考えられません。
MESを導入することで、経験則にもとづいた手書きのメモによる作業連絡などがなくなり、こうした現場のリアルタイムの情報が本社や各拠点間でも共有できるようになります。また、MESを基幹システムと連携することで、実績入力などの間接工数を削減でき、より一層手入力によるミスも大幅に削減されます。
さらにMESによって設備情報をデータで取得、管理できるので、消耗品の交換時期や設備そのものの保全を適切なタイミングで実行できるようになります。そのため大規模な故障や停止が起きるリスクが減り、保全のための人員も最低限に抑えることが可能です。
さらにMESによって生産状況をリアルタイムに監視でき、異常発生時はアラートが発せられる仕組みとなっているため、迅速、正確な対応がしやすくなります。
顧客からのクレームが発生した場合でも、データで生産状況を把握しているため、問題となっている部品やロットを発見し、すぐに調査が可能です。そのため再発防止策を打ちやすくなり、顧客からの信頼回復も容易になるでしょう。
MESを構成する11の機能
アメリカのMES推進団体である「MESA International」によると、MESの機能は11の機能に区分されています。ここでは、各機能の内容を要約して解説します。
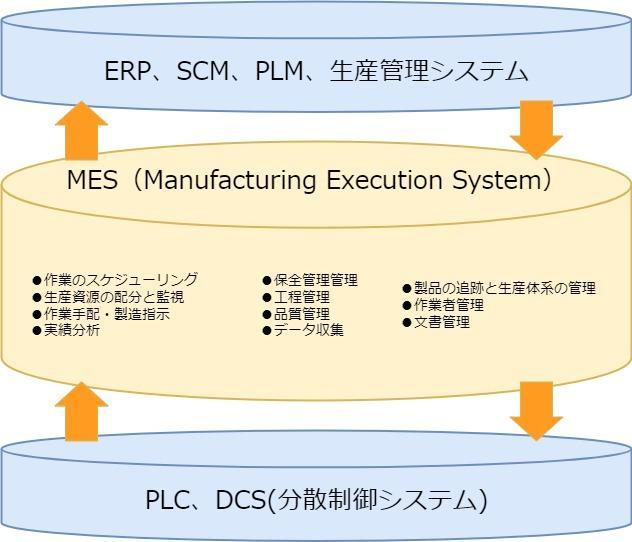
1.生産資源の配分・監視(Resource Allocation & Status)
設備や工具、人といった生産資源を、製造を開始する前に準備して、整える機能。資源の情報を把握して、正しく配分されているかなどを監視する。
2.仕様・文書管理(Document Control)
製造には、図面や作業指示書などを作成し、製造記録を管理する機能が必要となる。製造工程で必要な書類が自社の基準を守っているかといったことや、蓄積した書類を適正に管理できているかも重要となる。
3.作業スケジューリング(Operations/Detailed Scheduling)
ERPなど上位層で策定した生産計画をベースに、生産ラインを動かす上で必要になる詳細なスケジュールを立案する機能。生産プロセスや、設備、人の割り当てなども決めていく。
4.差立・製造指示(Dispatching Production Units)
作業者に対して指示を行う機能。製造指示をはじめ、仕様変更、仕掛品の管理などの情報も共有する。
5.作業者管理(Labor Management)
作業者の状況・状態を把握し、それに対する負荷を考慮した最適な割り当てを行う。生産スケジュールや機械の負荷状況なども合わせてリアルタイムでの情報共有が必要。
6.プロセス管理(Process Management)
生産工程の状況を把握して異常発生時の対応を支援する。即座に対応ができるよう、アラートなどの通知機能を用意し、プロセスごとの状況を常に把握する。
7.データ収集(Data Collection & Acquisition)
各工程の進捗状況把握のため、いつ・誰が・どのプロセスを作業したかといった情報を収集する。さらにこれらの情報から最適な人員配置などの分析も行う。
8.製品追跡と体系管理(Product Tracking & Genealogy)
仕掛品の進捗確認や製造履歴の情報を管理する。これらを把握することで実績管理だけではなく後工程などのスケジューリングにも役立つ。
9.実績分析(Performance Analysis)
不良発生も含めた実績データから比較や分析を行う。これにもとづいて進捗管理や出荷予測を行う。さらに出荷後も蓄積したデータから原価分析や作業工数の標準化計画を立てる。
10.品質管理(Quality Management)
製品の品質管理を実施する機能。検査業務の管理に利用する。蓄積された各種実績データや不良情報を活用し、適正な品質管理を行っていく。
11.保守・保全管理(Maintenance Management)
設備などの定期メンテナンスや予防保全に利用される機能。この機能により設備や機械のメンテナンスを確実に定期的に実行できるようになる。これにより想定外の設備の停止や不良の防止につながる。
(参考)History of the MESA Models
実際のところ、これらの機能がすべてそろっていなければMESと呼べないわけではありません。どの機能が必要になるかは、製造現場によって異なるため、各企業が自社のニーズに合った形でMESを構築していくのが一般的です。
たとえば、生産方式だけを見ても、受注生産と見込み生産、プロセス製造とディスクリート製造、ライン生産とセル生産、といったように多種多様であることから、どの企業にもマッチするMESはほとんどありません。自社に必要な機能が何か、また、その時にどういったデータを収集・管理すべきなのかをしっかりと定義した上で、システムを構築するようにしましょう。
MESを導入する5つのメリット
ここでは、製造業がMESを導入することで得られる、5つのメリットについて解説します。
【メリット1】自社のリソースをムダなく活用できる
【メリット2】ものづくりのQCD向上に役立つ
【メリット3】技能継承の課題を解決できる
【メリット4】多品種少量生産に対応できる
【メリット5】部門間連携がスムーズに行える
【メリット1】自社のリソースをムダなく活用できる
製造業は自社の限られたリソースをムダなく活用して、付加価値を高めていかなくてはなりません。基幹系システムよりも製造現場との距離が近いMESを導入すれば、生産設備や作業者をはじめとするリソースの空き状況を的確に把握し、リアルタイムに変化する生産計画や進捗状況に合わせた最適な形で作業割り当てを行えるようになります。
また、多くの製造現場は今でも紙の帳票やホワイトボードを使ったアナログな管理を行っています。アナログな管理にはムダが多く、作業者の負担も大きいものです。MESでは、タブレット端末やハンディターミナル、RFID(Radio Frequency Identification)タグを用いて、情報が書き込まれたICタグ・RFタグ(RFIDタグとも呼ばれる)とワイヤレス通信し、情報の読み取りや書き換えを行います。これらの記録業務を効率化する機器をよく採用しているほか、生産設備のPLCから直接データを吸い出して管理するといったことも可能です。貴重なリソースである作業者の事務作業的な負担が軽減されれば、本来の仕事である生産業務に集中できるようになるでしょう。
【関連記事】RFIDとは?特徴、仕組み、種類、機能やバーコードとの違いを解説
【メリット2】ものづくりのQCD向上に役立つ
製造現場には、ものづくりのQCDの向上が常に求められています。MESを導入して製造現場に関するあらゆるデータを収集・管理できるようになれば、QCDの向上に役立てることが可能です。
たとえば、MESに集まったデータを分析して生産設備のトラブルや異常を発見できれば、不良品の発生を未然に防げます。また、作業者や生産設備の空き状況を踏まえてムダのないスケジュールを組めるようになるので、コスト削減や納期の短縮を実現できます。
【メリット3】技能継承の課題を解決できる
日本企業のものづくりは今でも熟練技術者の勘や経験に頼っている部分が多く、属人化が進んでいます。昨今の人手不足によって若手人材が確保しにくいという背景もあり、技能継承が大きな課題と考えられてきました。しかし、MESがその課題の解決に役立つと期待されています。
MESには、製造現場でのものづくりに関するあらゆるデータが集約されており、その中には、熟練技術者のスキルやノウハウも含まれています。熟練技術者がこれまで勘や経験で行っていた作業をほかの作業者に共有したり、生産設備で自動化したりできるようになれば、ものづくりの力はさらに高まっていくでしょう。
【メリット4】多品種少量生産に対応できる
製造業は、かつての「大量生産」から「多品種少量生産」の時代へと切り替わっています。大量生産の時代は、同じ製品を効率的に作ることだけを意識すればよかったので、高度な生産管理はあまり必要とされてきませんでした。しかし、多品種少量生産の時代では、市場のニーズの変化に合わせて生産量を調整し、数多くある製品の在庫数を適正に保ちながら生産していかなくてはならず、高度な生産管理が求められます。
従来の生産計画は、熟練担当者の知識や経験に頼っている傾向にありました。しかし、多品種少量生産の複雑な生産計画をすべて人の手で行うのは極めて困難であり、システムによるサポートが必要になります。MESのように製造現場の情報が集約されたシステムを活用することで、製造業は多品種少量生産にも柔軟に対応できるようになるでしょう。
【メリット5】部門間連携がスムーズに行える
MES(Manufacturing Execution System)は、部門間連携をスムーズに行うための重要な役割を果たします。
MESは生産プロセス全体を統合的に管理し、生産計画、在庫管理、品質管理などの情報をリアルタイムで共有し、一元管理することができます。これにより、異なる部門間での情報共有や関係部署間の連携がスムーズになり、コミュニケーションが円滑化されます。また結果的に、QCDの向上にもつながります。
さらに、部門間連携が円滑化することで情報共有やコミュニケーションがスムーズになり、組織全体の効率性と生産性の向上につながります。各部門が一体となり、共通の目標に向けて連携しやすくなると考えられます。ひいては意思決定の迅速化、生産ラインの最適化、顧客満足度の向上などにつながり、企業の競争力の強化に繋がるといえるでしょう。
MESの代表的なサービス
ここでは、MESの代表的なサービスを紹介します。
CCT「Orizuru Mes」
OrizuruはIoT技術により製造現場のさまざまな状態をデータ化・可視化、AIを活用して課題解決するMES。生産性の向上・業務効率化を実現します。またベテラン従業員の業務をデータ化して蓄積することで自動化を可能にし、属人性低減・省人化が可能になります。
既存の設備・業務フローは企業により多種多様ですが、CCTでは導入前の業務コンサルティングから運用時の体制支援まで対応可能です。
(公式)Orizuru
TOPiCS-X
TPiCSではfMRP製番管理システムを提供しています。繰返生産や、少量多品種・個別一品受注生産が混在していても生産管理できる、画期的な製造業システムです。またカスタマイズ性が高く、さまざまな企業の個別事案にも対応できる点も強みです。
(公式)TPiCS
Panasonic「MES ソリューション」
パナソニックの提供するMESシステム「MESソリューション」は、製造業におけるさまざまなノウハウを「蓄積・形式知化・活用」することで、QCDを継続的に改善できるシステムです。顧客の課題や要望ごとに開発されるハーフ・スクラッチ型のため、あらゆる企業へ最適化されたシステムを提供できます。パナソニックグループへの導入事例が多くなっているため安心感があります。
WorkGearシリーズ
WorkGearシリーズは工場で必要な見積・受発注から、売上仕入・売掛買掛までトータルで機能する生産管理システムです。特に中小企業に向けて最適化させており、導入実績が多くなっています。
(公式)【WorkGear-X・XZ】中小製造業向け生産管理&業務総合システム
MESシステム導入の課題
導入目的や業種によって、同じMESシステムでもその企業に最適なMESは異なります。実際に導入する際は、ある程度ポイントを絞って検討し、ミスマッチを防ぐことが必要です。
確認すべきポイントは、以下の5つになります。
- 必要とする機能を備えているか
- 自社の業界に適したシステムか
- 複数拠点での対応が可能か
- 操作性が高いか
- サポート体制が充実しているか
またコスト面においては、当然経営陣を説得しなければなりません。長期間で導入後の効果が期待できるかなど、論理的な内容が必要です。同時にDXという「えたいのしれないもの(と、古くからの経営陣や技術者たちは思っていることが多い)」に対する不安や懸念、デメリット、リスクをできるだけ払拭しなければなりません。
そのためには、どのように・どの部門から導入するのかも考え、計画を進める必要があります。
【関連記事】
4つのMESを徹底比較|見るべきポイントや必要な機能を解説
さらなる普及が期待されるMES|今後求められる新たな機能・役割
製造業DXに欠かせないMESは、今後さらにその機能を拡張させて運用する必要があるとされています。それは複数の工場を持つ製造業企業が、各工場に最適なMESを構築・運用するのではなく、すべての生産現場を統合して管理できるMESを構築し、すべての生産設備全体で最適化を図るというものです。
もともと、各生産現場は“それぞれ(生産現場ごと)の状況把握”のためにMESを導入していることがほとんどです。たとえば、「A工場がB工場にある在庫の状況を把握し、さらにB工場の業務に支障のない形で在庫を融通してもらう」といったことは現状では不可能です。
しかし“すべての生産現場を統合して管理する”MESを構築することで、予定外の注文に手持ちの在庫では応えられないといった状況でも、各生産現場の情報を即座に把握して、自動的に必要な在庫を融通できるようになります。
これは、生産現場ごとに分断されている各制御システム(OT)をITでつなぐ、という言い方もできるでしょう。これによって可能になるのは工場の「スマートファクトリー化」です。つまり、現実にはそれぞれの場所に位置する各工場を、仮想的にまるで一つの大工場のように管理、運用するということになってきます。
【関連記事】
スマートファクトリーとは?メリットと成功のポイント、導入事例を解説
まとめ
この記事では、製造業のDXに役立つMES(製造実行システム)について解説しました。MESは、生産設備との連携により、各工程の稼働状況や生産量をリアルタイムで把握し、生産計画の進捗状況を可視化することで製造工程の効率化を図ります。さらにMESは、SCM(サプライチェーンマネジメント)システムやERPシステムとの連携により、企業全体の業務効率化を促進します。
近年では、IoTやAIの技術革新によってMESの機能はますます高度化しており、予知保全や生産における自動化など新たな可能性が広がっています。MESを導入することで、製造業は市場の変動に迅速に対応し、高品質な製品を効率的に生産することが可能になります。
MESを導入することで、製造業が担う「ものづくり」はさらに進化していくでしょう。本コラムを参考にしつつ、MESの導入を検討していただければ幸いです。
【注目コンテンツ】
・DX・ESGの具体的な取り組みを紹介!専門家インタビュー
・DX人材は社内にあり!リコーに学ぶ技術者リスキリングの重要性
・サービタイゼーションによる付加価値の創造と競争力の強化