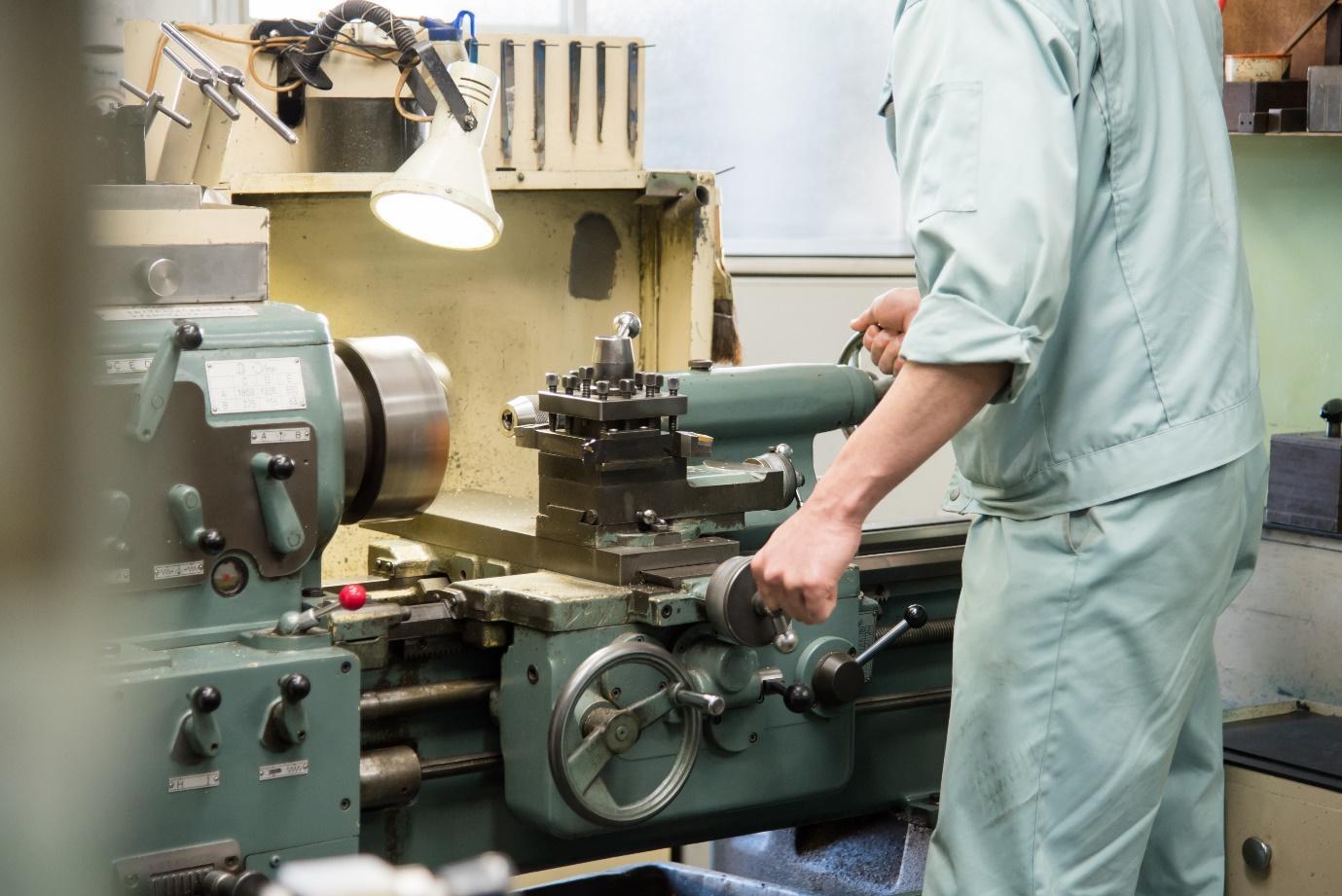
生産現場の効率性に悩む経営者や現場担当者の方は少なくないでしょう。このような課題を解決する上で役に立つのがインダストリアルエンジニアリング(IE)です。複雑で理解しにくいとも言われるこの手法について、体系的かつわかりやすく解説します。
目次
インダストリアルエンジニアリング(IE)とは?
インダストリアルエンジニアリング(IE)とは、1800年代の終わりに生まれた学問領域のことです。現代では、業務効率化や業務改善に用いられる手法として広く知られています。省力化や業務時間の短縮につながる手法のため、生産現場だけでなくサービス産業や家庭生活の中でも活用されている傾向です。
インダストリアルエンジニアリング(IE)の定義
インダストリアルエンジニアリングは、英語でIndustrial Engineeringと書き、和訳すると「生産管理工学」です。日本インダストリアル・エンジニアリング協会では、インダストリアルエンジニアリングを以下のように定義しています。
IEは、価値とムダを顕在化させ、資源を最小化することでその価値を最大限に引き出そうとする見方・考え方であり、それを実現する技術です。
引用:日本インダストリアル・エンジニアリング協会
これは、作業工程・内容を科学的な手法を用いて分析し、より最適あるいは効率的とも言える方法を見つけ出すことを意味します。主に、製造業の現場で活用されています。また近年は、事務作業の改善や経営管理のほか、人や情報などを対象とした幅広い分野で用いられるようになっています。
インダストリアルエンジニアリング(IE)のメリット
インダストリアルエンジニアリングは、製造業の現場などにおいてムダやムラなどを削減し、生産性の向上や業務改善を図ることを目的に実施されます。
業務改善においてインダストリアルエンジニアリングを活用するメリットは以下の4点です。
- 科学的な分析手法を用いるため、実施する人によって分析結果が変わる心配がない
- 記号や図表などを活用することで、客観的な視点で無駄を洗い出せる
- 従業員の課題解決に対する意識を高めることができる
- 生産性の改善により、顧客のニーズを満たす製品を低コスト・期限内に造ることが可能となる
(出典:JISリスト - JISC 日本産業標準調査会)
インダストリアルエンジニアリング(IE)手法の3タイプ
インダストリアルエンジニアリングの手法は「方法研究」「作業測定」「それらの組み合わせ」の3つに大別されます。ここでは、それぞれの目標と具体的な手法を解説します。
方法研究の目的とその手法
方法研究とは、JISによると「作業または製造方法を分析し、標準化・総合化によって作業方法や製造工程を設計・改善する手法の総称」とされています。加工などの工程や生産・運搬などの作業を分析し、業務を改善するための具体的な方法を見つけ出していきます。
方法研究でより良い方法を見つけるために「工程分析」や「動作研究」などが行われます。JISの定義によると、動作研究は「作業者が行うすべての動作を調査・分析し、最適な作業方法を求めるための手法の体系」です。これを実現するために有効なのが、身体の使用、作業者の配置、設備や工具の設計をもとに考えられた「動作経済の基本原則」を守ることです。
<動作経済の基本原則>
原則1:動作の数を少なくする
原則2:両手を同時に使う
原則3:移動の距離を短縮する
原則4:動作を楽にする
また工程分析は「生産対象物が製品になる過程、作業者の作業活動および運搬過程を、対象に適合した図記号で表して系統的に調査・分析する手法」とJISで定義されています。具体的には、以下のような記号によりモノの流れを表すことが可能です。
作業測定の目的とその手法
作業測定とは、JISによると「作業・製造方法に関する実施効率の評価や、標準時間の設定を行うための手法」とされています。定量的に作業時間を測定したり、作業の標準時間を設定したりします。作業測定で作業の効率や時間を調べるには、「時間研究」や「稼働分析」などが必要です。
時間研究は「作業を要素作業または単位作業に分割し、その分割した作業を遂行するのに要する時間を測定する手法」とJISで定義されています。具体的な手法の一つが、ストップウォッチ法です。この手法は、ストップウォッチで各作業の要素にかかる時間を測定し、最大値や最小値、平均値などを求め、結果から作業や動作の改善を図るというもの。
また稼働分析は「作業者または機械設備の稼働率、もしくは稼働内容の時間構成比率を求める手法」とJISで定義されています。稼働分析をすることで、作業者数や機械台数、作業量などの適切な算定に役立てることが可能です。分析をするうえで、まずは作業を以下の3つに分けましょう。
1. 稼働:付加価値を生じる作業
2. 非稼働:付加価値を生じない作業
3. 準稼働:付加価値を生んでいないが、現状のシステムでは必要な作業
特に「準稼働」に分類される作業は、システムを変えるだけで削減できることがあるため、最初に改善を図る対象とします。
組み合わせ
方法研究と作業測定を組み合わせた手法には、以下の3つの方法があります。
- MMチャート(マン・マシン・チャート)
- ラインバランシング
- DI分析
MMチャートとは、人と機械で行う作業の効率を高める手法です。「人と機械が共同で作業する連合作業」「別々の作業をする単独作業」「手待ちや機械の停止部分に当たる不稼働」の3つに分類し、手待ちの原因究明や効率化に役立てます。
【MMチャートの例~作業を可視化して改善案を導き出す~】
JISの定義によると、ラインバランシングとは「生産ラインの各作業ステーションに割り付ける作業量を均等化する方法」です。異なる作業工程における作業時間のバラツキによる手待ちを解消することを目的としています。作業編成の変更や作業工程の削減により、作業の短時間化や省力化を図ることが可能です。
DI分析は、DistanceとIntensityの頭文字を取った分析方法で工程間の距離と運搬強度(運搬量や運搬回数など)からレイアウトを改善します。すべての運搬を可視化し、流れや距離、強度を定量化することで改善すべき運搬対象を明確にできることが特徴です。レイアウトを最適化することで、労力の削減や時間短縮につながります。
インダストリアルエンジニアリング(IE)を利用した改善事例
インダストリアルエンジニアリングは、多くの業界で活用されていますが、主に製造業で発展してきた技術です。ここでは、インダストリアルエンジニアリングを利用した製造業の改善事例を解説します。
トヨタ生産方式もインダストリアルエンジニアリング(IE)手法
トヨタの「トヨタ生産方式」もインダストリアルエンジニアリングをもとに設計されています。インダストリアルエンジニアリングは「経営目的を定め、それを実現するために、環境との調和を計りながら、人や物、金および情報を最適に設計・運用し、統制する工学的な技術・技法の体系」(日本産業規格)です。
トヨタ生産方式では、「お客様にご注文いただいたクルマを、良い品質で、安く、タイムリーにお届けするために、徹底的にムダをなくし、リードタイムを短くする」(トヨタ)という目的があります。この目標を達成するため、「ニンベンのついた自働化」「ジャスト・イン・タイム」の2本柱をもとに人や物、金および情報を最適に設計、運用して自動車を製造しています。
トヨタ生産方式の説明の中では「インダストリアルエンジニアリング」という言葉を用いていませんが、考え方の根幹にはインダストリアルエンジニアリングがあるものと考えられます。
自動車パーツ製造会社での改善事例
九州にある自動車パーツ製造会社は、インダストリアルエンジニアリングの考え方に則って、DXや「100年に1度の変革期」へ対応。同社は、DXを推進する中でコストと人に関する問題を抱えていました。例えば20年以上稼働している設備を抱えていましたが、それらをデジタル化対応機器へ一新すると大きなコストがかかります。
また人の問題では「デジタルツールを導入しても使いこなせない人がいる」という問題を抱えていました。これらの経験から「デジタルで可能なこと」と「現場が求める効率化」は、必ずしも一致せず、ユーザーに寄り添い身の丈に合った効率化が重要だと気づくことに。このように自社に必要なデジタル化を見抜いてDXを推進したことで、年950時間の省力化を実現できました。
大手電子機器製造業者による改善事例
日本の大手電子機器製造業者は、インダストリアルエンジニアリングを活用して現場の作業を可視化し、目標値とのギャップを定量的に確認できる仕組みを取り入れています。これにより「可視化・標準化・実行・課題の特定と改善」のサイクルを円滑に回せるようになり、日常的な業務改善ができるようになりました。
さらに同社は、サプライチェーンの現場でもインダストリアルエンジニアリングを活用しています。IoTにより収集したデータを解析することで作業中の課題を特定し、ボトルネック工程の改善に役立てています。また各作業現場の状況のデータをリアルタイムに収集し連携することで、トラックの積み込み作業で発生する待ち時間を削減する取り組みも推奨中です。
インダストリアルエンジニアリング(IE)を実施する際に役立つ考え方
インダストリアルエンジニアリングを実施する際には、「ECRSの原則」と「5W1H」の考え方が役に立ちます。この章では、それぞれの考え方を簡単に紹介します。
ECRSの原則
JISによると、ECRSの原則とは『工程、作業、動作を対象とした分析に対する改善の指針』とされています。 インダストリアルエンジニアリングでは、工程分析などで見つかった問題点を改善する具体的な方法を考える際に役立ちます。
ECRSの原則では、以下の問いかけを行うことで改善の方法を検討します。
- Eliminate(排除):作業や工程を無くせないか
- Combine(結合):作業や工程を1つに集約できないか
- Rearrange(交換):作業や工程の順序・場所を入れ替えできないか
- Simplify(簡素化):作業や工程の簡素化・単純化できないか
一般的には、E→C→R→Sの順に改善の効果は小さくなると言われています。したがって、改善の方法を検討する際もこの順番で問いかけするのがおすすめです。
5W2H
5W2Hとは、5W1HにHow muchを加えたフレームワークのことです。具体的には、以下の7つの要素によって構成されています。
1. When(いつ?)
2. Where(どこで?)
3. Who(誰が?)
4. What(何を?)
5. Why(なぜ?)
6. How(どうやって?)
7. How much(いくらで?)
インダストリアルエンジニアリングを実施する際には、5W2Hを意識すると目的に沿った漏れのない運用が可能になります。5W1Hに基づいてIEの活動を行うことで、客観的な視点で改善すべき部分や改善方法を検討できるでしょう。
インダストリアルエンジニアリング(IE)の資格
インダストリアルエンジニアリングに関連する資格は「技術士」「IE士」の2つがあります。それぞれの特徴を解説します。
技術士
技術士は「科学技術に関する技術的専門知識と高等の応用能力及び豊富な実務経験を有し、公益を確保するため、高い技術者倫理を備えた、優れた技術者」の育成を図るために設置された国家資格です。技術士は、21の技術部門を網羅しており、インダストリアルエンジニアリングは特に「経営管理/数理・情報」を学ぶ経営工学部門と関連しています。
試験は、筆記試験のみの一次試験と筆記試験と口頭試験がある二次試験の2つで構成されています。近年の二次試験の合格率は約10~15%であり、難易度の高い試験といえるでしょう。
参考:日本技術士会
IE士
インダストリアルエンジニアリングに関連する資格には、JMA(日本能率協会)が管轄するIE士という民間資格もあります。IE士の講習では、インダストリアルエンジニアリングの概念から実践的な改善手法までを広く習得可能です。現場で使える分析シートや、部分最適から全体最適の考え方を学べるため、実践にもすぐに役立てる内容といえます。
参考:日本能率協会「生産革新プロフェッショナルコース(IE士養成コース)」
インダストリアルエンジニアリングによって業務の改善を図ろう
インダストリアルエンジニアリングを実施することで、動きや工程のムダを無くしたり、作業時間の最適化を図ったりできます。結果として、生産性の改善や従業員の課題解決に関する意識向上などの効果も期待できます。
インダストリアルエンジニアリングの手法は、「方法研究」と「作業測定」の2種類に大別され、それぞれ複数の手法に細分化されます。そのため、まずは方法研究と作業測定の全体像を把握した上で、各手法の使い方やメリットなどの理解に努めた方が、よりスムーズに理解できるでしょう。
PwCコンサルティングが経済産業省の委託を受けてまとめたレポートによると、トヨタ自動車が工場IoTを実施する目的の1つに「インダストリアルエンジニアリング化されていない設備の標準化」を挙げています。デジタル技術を使ったトヨタ生産方式の実現を目指す中で、インダストリアルエンジニアリングがキーワードになっています。
今回紹介した内容を押さえた上で、製造や事務などの作業に関する生産性や効率性の向上を図ることで、より効率的な企業経営ができるようになるでしょう。
【注目コンテンツ】
・DX・ESGの具体的な取り組みを紹介!専門家インタビュー
・DX人材は社内にあり!リコーに学ぶ技術者リスキリングの重要性
・サービタイゼーションによる付加価値の創造と競争力の強化