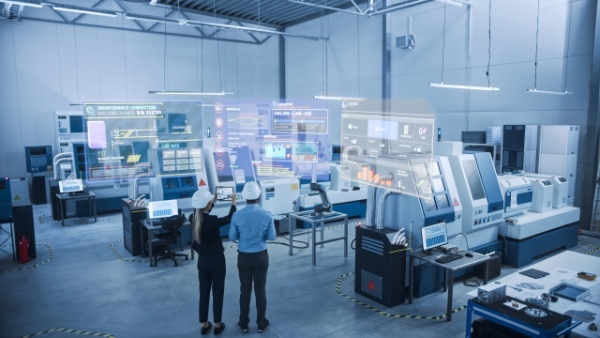
デジタルマニュファクチャリングとは、先端技術を活用して生産プロセスを最適化する取り組みやプロセスを指します。本記事では、デジタルマニュファクチャリングの概要、製造業に取り入れられる背景、そのメリットや事例について詳しく解説します。
目次
デジタルマニュファクチャリングとは
従来の製造現場は「モノづくりをするところ」と定義されていました。しかし、これからは違います。今後はモノをつくり、製造過程のデータを収集するだけでなく、出荷後の販売データやアフターメンテナンスのデータも収集していくことで、より自社クライアントや最終消費者の要望に合った製品や部品を製造していくための「モノづくり+データづくり」として機能していくことが製造現場に求められているのです。
このように、モノづくりだけでなく、納品後に収集するデータも併せて活用し、生産性向上、品質向上、リードタイム短縮を実現するとともに、よりクライアントのニーズに近い製品を生産していくことを「デジタルマニュファクチャリング」といいます。
調査会社のReport Oceanが2022年3月に発表したレポートによると、アジア太平洋地域のデジタルマニュファクチャリング市場はIoTやロボティクス、製品ライフサイクル管理(PLM)、デジタル人材採用の増加などの要因で、2022年から2031年までに期間で年平均16.8%の成長を遂げ、2031年には1兆1963億ドルになると予測しています。
日本の製造業でもDXは急務ですが、世界規模で製造業のデジタル化が進んでいることがわかります。
デジタルマニュファクチャリングの種類
デジタルマニュファクチャリングには、大きく分けて以下の3つの種類があります。
プロダクト・ライフサイクル(製品ライフサイクル)
プロダクト・ライフサイクルは、製品が開発されてから廃棄されるまでの全体的な過程を指します。デジタルマニュファクチャリングにおいては、プロダクト・ライフサイクル全体をデジタル化し、製品の設計、調達、生産、販売、保守などの各段階でデジタルデータやデジタルツールを活用します。具体的には工程をデータで一元管理ができるPLM(Product Lyfecycle Management)が活用され、製品の開発と製造の効率化、原材料の需要予測、設計仕様の修正など品質の向上、顧客ニーズに合わせた柔軟な製品やサービスの提供が可能となります。
関連記事:【製造業DX】「PLM」とは?~製品ライフサイクルをデータ管理し、製品開発力の強化につなげる製造業DX手法~
スマートファクトリー
スマートファクトリーは、IoT(Internet of Things=モノのインターネット)やAI(Artificial Intelligence)などの先端技術を活用して生産工場を自動化・最適化する概念を指します。デジタルマニュファクチャリングでは、スマートファクトリーを実現するために生産設備や製造プロセスをデジタル化し、リアルタイムのデータ収集と分析を行います。これにより、生産能力の向上、品質管理の強化、コスト削減が実現できます。
関連記事:スマートファクトリーとは?製造業の事例と導入のメリット
サプライチェーン・マネジメント
サプライチェーンとは、原材料の調達から製造、在庫管理、配送、顧客に届くまでの製品やデータの一連の流れのことで、サプライチェーン・マネジメントとはその一連の流れを最適化するために効率よく管理することです。
グローバル化が進み、複雑化するサプライチェーン全体を一元管理するには、デジタル化が必須といえます。リアルタイムでモノと情報、お金の流れを把握することで、スピーディで正確な経営判断が可能となります。人材不足が叫ばれて久しい製造業において、生産性向上や無駄を無くすことにもつながるため、サプライチェーン・マネジメントはデジタルマニュファクチャリングを進めるにあたり、非常に重要な要素となります。
関連記事:サプライチェーンとは?マネジメントの必要性と成功のポイント
デジタルマニュファクチャリングに求められる技術
DXやデジタルマニュファクチャリングを実現するためには、IoT、AI、RPAなど、これまで製造現場ではあまり見られなかった新しい技術を取り入れることが必要です。
たとえば、RFIDタグの活用をイメージしてみましょう。RFIDタグを使えば、ID情報を埋め込んだRFタグから、電磁界や電波などを用いた近距離の無線通信によって情報を得ることができます。
自動車部品の例では、一定以上の大きさの部品にはRFIDタグを埋め込んでおくことで出荷後どころか、自動車に組み込まれた後、さらには街の中を走り解体された後でも、その部品が「いつ」「どの工場で」製造され、「どのクルマの」部品として使われていたのかなどを把握することができる、すなわちトレーサビリティが実現するのです。
RFIDという従来からある技術と近年急速に進歩しているIoT技術を組み合わせることにより、「出荷まで」だけでなく「出荷後」の管理が実現できます。製品そのものの価値だけでなく、その製品に付随するデジタル情報の価値をも付加することができるため、クライアントの満足度をより高めたり、製品単価を上げたりすることができるでしょう。

このように製造業におけるDXとは、単純にロボットやシステムを現場に導入するということではありません。すべての製造プロセスや出荷後のデータを一元管理し、現場にフィードバックすることで、生産性と安全性が高く、製造コストが低く、そして何よりもクライアントに満足していただけるようなモノづくりができるようにすることを指すのです。
関連記事:トレーサビリティとは?仕組みや活用方法を簡単に解説
製造業DX(デジタルトランスフォーメーション)とは
ここであらためてDXについて解説します。現在、日本だけでなくすべての国の製造現場においてあらゆる変革が求められています。変革を実現するためには、モノづくりの現場において、これまで培ってきたノウハウを従業員個人の経験値として頭と身体に蓄積するだけでなく、デジタル化により共有しやすくすることで、リードタイム短縮、生産性向上、品質向上などに生かしていくことが必要です。これらのデジタルデータを活用して製造現場を変革していくことを、総称して「DX(デジタルトランスフォーメーション)」といいます。
DX推進の流れは昨今のコロナ禍の影響により、そのスピードは急激に加速し、市場規模が拡大していると言われています。製造業のビジネス現場において、DXの実現は、もはや必須のものとなると考えられます。
デジタルマニュファクチャリング、製造業DXが求められる4つの背景
DXやデジタルマニュファクチャリングが経済全体、また製造業に求められている背景(理由)には、以下の4点が挙げられます。
【理由1】労働人口の減少
日本では少子高齢化が進んでいます。労働人口が減少していると叫ばれて久しく、出生率も上がらない状況において、今後も人的リソース不足が続いていくことは確実視されています。
その中でも特に製造業は、肉体労働できついイメージ、機械などが危ないイメージ、単純作業でつまらないイメージ、上下関係など人間関係が厳しいイメージなどがあり、恒常的な人出不足の傾向があります。人の手が必要な作業をできるだけ減らすことは急務と言えるでしょう。
【理由2】設備・システムの老朽化
製造業企業で使われている設備やシステム関係が古く、不具合が生じる、古くて効果効率を期待できない、新しく導入するシステムと連携できないなどの問題が生じています。
古いものでも維持やメンテナンスにお金や手間がかかり、だからといってできることが多い訳ではないので、生産性を上げるためには、企業は新システムへの移行は急務と言えます。
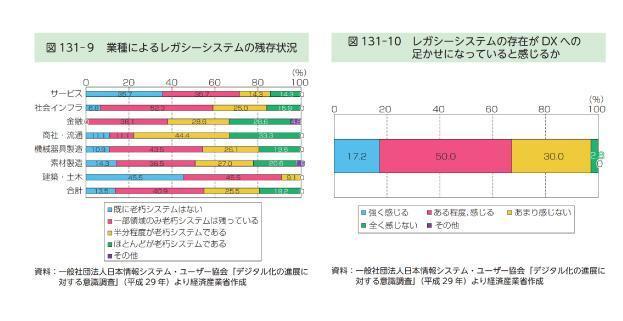
【理由3】新しい働き方への対応
2019年の法改正を契機に「働き方改革」が叫ばれ、また2020年の新型コロナ感染症の蔓延も後押し材料となり、時間や場所にしばられない新しい働き方を認め推奨していくことは、企業側に求められている重要事項の一つと言えます。
フレックスタイムの導入やリモートワーク、育児や介護の休暇といった多様な働き方を具体的に導入し、運用していくには、属人化しない仕事の仕組み化、システムによる管理が求められることになります。
【理由4】新興勢力・海外勢力とのコスパ競争
中国や韓国、東南アジアなどの企業が、安い労働力や原材料費を武器に、低価格な製品販売を行う流れが年々高まっており、これからの製造業は、それらの勢力と戦い勝つ必要があります。
コストパフォーマンスを上げるには、高い品質を実現するか、低価格に抑えるかのいずれか、または両方が求められます。そのためには、既存の製品を見直しグレードアップさせることのほか、製造工程を見直し効率化させるなどを行うことが考えられます。しかし、そのためには既存の製品や使用シーンの可視化、データ化が求められることとなります。
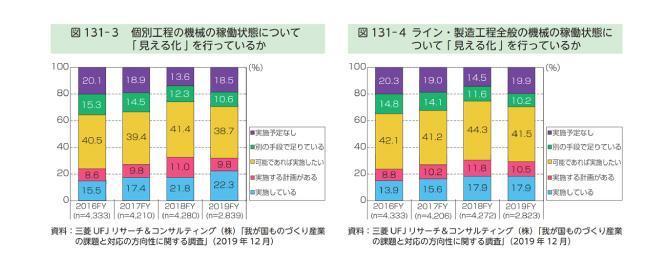
デジタルマニュファクチャリングの事例
ここでは、デジタルマニュファクチャリングの事例を紹介します。
部品工場のトレーサビリティについて|部品工場の例から
たとえば、ある自動車用の部品を生産している工場の取り組みを見てみましょう。多くの製造現場では、生産個数、完成品の品質、出荷個数などの「その部品が工場で作られ、出荷されるまで」の情報しか管理ができないという課題があります。
この場合、その部品が組み込まれた自動車に故障が発生し、おそらくこの部品が不具合の原因だろうと特定された場合でも、「その部品が生産されたであろう工場」までしかさかのぼることができません。しかし、この部品に「トレーサビリティ」と呼ばれる、「どの工場でいつ生産されたものか」という情報が入っていたらどうでしょうか?
不具合が発生した原因と思われる部品を製造した工場において、その部品を作り出すための鉄の溶解温度、冷却温度とその所要秒数、ドリルの回転速度などの「生産環境を記録したデータ」を後から呼び出すことができれば、なぜそのような不良品が出来上がってしまったのかなどの原因が特定できるでしょう。また今後同様の不具合発生を防止すべく、対策を施し、生産管理を行うこともできるようになります。
その他の事例
上記以外にも、以下のようなシチュエーションと解決法が考えられます。
- 製品の検品や外観検査にAI技術を導入し、検査員のリソース不足や、人間の目視による検査で生じる誤りやバラツキをなくし、且つ時間短縮、スタッフの別業務充当を図る。
- 製品の生産ラインにAI音響解析を導入し、熟練者の耳に頼ることなく、異常音を検知することで不良を軽減する。
- VRやAR、MR技術を研修や従業員育成に導入し、現場で起こり得る状況を再現しつつ、高い精度のトレーニングを行うことで、生産効率の向上と不良率の低下を図る。
- 建設機械に位置情報を取得する衛星測位システム、制御するコントローラー、慣性計測装置などを設置し、データを本部に共有。遠隔地からでも正確な状況を把握する。
成功事例を見ていくと、特に製造現場におけるデジタルトランスフォーメーションでは、「その商品や部品の出荷時」までの品質を担保する必要があったことがわかります。具体的には以下のようなものが挙げられます。
- 「出荷後」の品質まで追いかけることができるようにする
- 不良品が発生した際にその不良品を製造してしまった環境を呼び戻し、どこに問題があったのかを特定する
- 同じ不良品を作らないための対策を施すことができるようにする
このほか、部品の検査をこれまでは熟練の検査員が目視で行っていたものを、データ化することで人的リソースに頼らない現場づくりができた例があります。合格の基準をスコアリングすることで条件ごとにAIがポイントをつけ、人の目だけに頼らない仕組みを作り大幅な効率化を果たした例です。高い技術をもつ熟練者の数は年々減っていることから、その貴重な技術をデータとして蓄積させ、未来への技術承継に役立てる手段は今後ますます必要になってくるでしょう。
デジタルマニュファクチャリング、製造業DXの実現のポイント
デジタルマニュファクチャリングおよび製造業のデジタルトランスフォーメーションを実現するための重要なポイントについて解説します。
AI
AIはデジタルマニュファクチャリングにおいて重要な役割を果たします。AIを活用することで、製造プロセスの最適化、品質の均一化、品質管理体制自体の質の向上、技術の承継、安全性の向上などが可能となります。機械学習やディープラーニングなどのAI技術を組み合わせ、データから傾向やパターンを抽出し、効率的な意思決定や予測を行うことは、今後日本の製造業が生き残るためには必須と言っても過言ではありません。
IoT(モノのインターネット)
IoTは、製造業におけるDXの鍵となる技術です。センサーやデバイスを組み込んだ製造設備や製品から、リアルタイムなネットワーク接続によってデータ収集を行い、分析することで、生産ラインの監視や制御、効率化が可能となります。
関連記事:製造業におけるIoTとは?導入のメリットと活用方法・事例を解説
プラットフォーム(基幹システム)の選定
DXの実現には、AIやIoTなど、新しい技術を取り入れることが必要とお伝えしました。新しい技術を取り入れるためには、技術導入のための資金確保、IT人材の採用、設備の導入、従業員への教育や製造現場への組み込みなど、多くのハードルを越える必要があります。これと同時に重要なのが、それらの新しい技術やサービスを管理するための「プラットフォームの選定」です。
製造現場におけるIT化やデジタルデータ採取にとどまらず、製造部品の調達、原価管理、販売データ、営業データ、顧客管理など、すべての情報を一元管理できるような業務システムを導入・最適化することができれば、DX戦略の成果をさらに大きくすることができるでしょう。
まとめ:デジタルマニュファクチャリング実現のポイント
この記事では、製造業におけるデジタルマニュファクチャリングについて解説しました。デジタルマニュファクチャリングは、製造業におけるDXの重要な要素であり、AI、IoTなどのテクノロジーを活用して製造プロセスを最適化し、効率性、品質、柔軟性を向上させる取り組みです。デジタルマニュファクチャリングに取り組むことで、企業は競争力を高め、市場の変化に対応し、持続的な成長を実現できるでしょう。
今後、製造業だけでなくすべての業種においてDXへの取り組みは加速していくと思われます。ぜひ、自社にはまだ早いと考えず、製造業だけでなく他業界も含めて、DXの取り組み成功事例を収集してみてください。
【こんな記事も読まれています】
・【会員限定動画】サプライウェブで実現するマスカスタマイゼーション時代の企業戦略
・製造業における購買・調達業務とは?課題の解決方法も紹介
・ビジネスや技術のトレンドに反応しながら進化を続けるCRMの事例を紹介