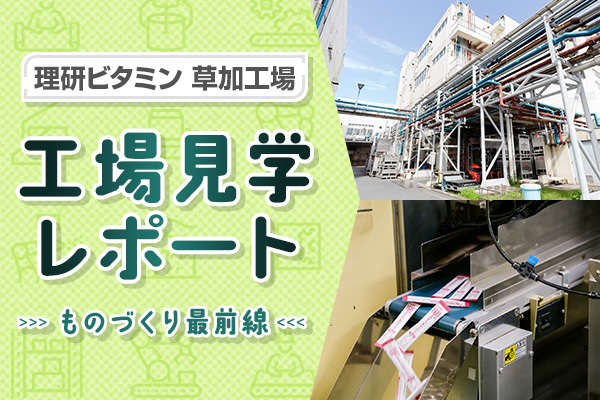
ノンオイルドレッシングやふえるわかめちゃん®、素材力だし®など、私たちの生活に身近な食品で知られる理研ビタミン。現在は食品と改良剤(食品・化成品)、ヘルスケアの3分野で事業を展開しています。
同社は首都圏と関西で計5ヵ所の工場を操業しており、埼玉県草加市の草加工場は食品部門の主要工場です。年間約3万トンの調味料を作っていますが、数年前より工場の生産担当者みずから省エネやDXに取り組んでいます。こうした取り組みが高く評価され、2020年度に省エネ大賞(経済産業省主催)、2021年度にはIT賞マネジメント部門(IT協会)を受賞しました。このように早くからDXを推進してきた草加工場ですが、製造現場はどのように進化を遂げてきたのでしょうか。
コアコンセプト・テクノロジー(CCT)CTOでKoto Online編集長の田口紀成氏が、工場見学を通じて製造業DXの最前線に迫る本シリーズ。今回は、理研ビタミン草加工場の工場長・藤森厚氏を始め、DXプロジェクトメンバーの皆さんにお話を伺い、工場を見学しました。
2013年 食品素材開発部 部長
2014年 Guymon Extracts Inc.関係会社社長
2021年 草加工場 工場長 執行役員
2008年 草加工場製造課 係長
2018年 草加工場製造課 課長
2020年 草加工場生産技術課 課長
2023年 草加工場製造課 課長
2004年 草加工場生産技術課生産技術係
2011年 本社生産本部管理部生産管理チーム
2019年 草加工場生産技術課生産技術係 係長
2023年 草加工場生産技術課 課長
エネルギー管理士
2013年 草加工場製造課 主務
2021年 草加工場製造課 チーフ(主務)
2023年 草加工場生産技術課生産技術係 主務
2016年 草加工場生産技術課生産技術係 主事
エネルギー管理士、公害防止管理者(水質・大気)
2002年、明治大学大学院 理工学研究科修了後、株式会社インクス入社。2009年にコアコンセプト・テクノロジーの設立メンバーとして参画し、3D CAD/CAM/CAEシステム開発、IoT/AIプラットフォーム「Orizuru」の企画・開発などDXに関する幅広い開発業務を牽引。2015年に取締役CTOに就任後は、ものづくり系ITエンジニアとして先端システムの企画/開発に従事しながら、データでマーケティング&営業活動する組織/環境構築を推進。
目次
食品部門の主要工場は施設・設備の老朽化が課題
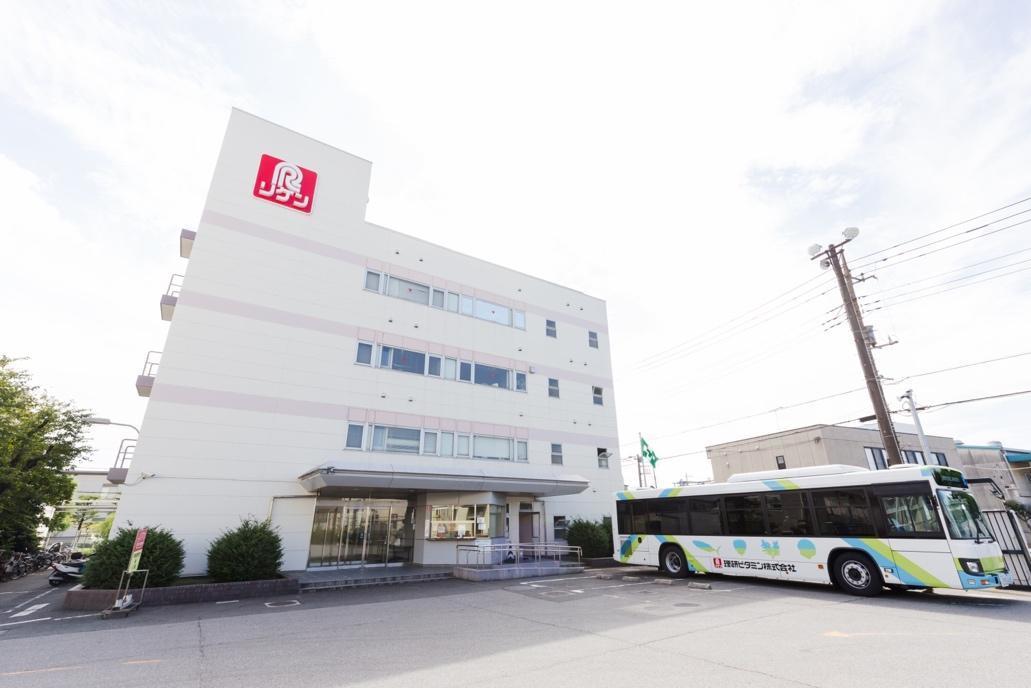
理研ビタミンの草加工場は1968年のラーメンスープの生産から始まり、現在はノンオイルドレッシングや素材力だしといった主力商品から和洋中の各種たれ・ソース・スープ類と幅広く調味料を生産しています。
田口氏(以下、敬称略) 最初に御社と草加工場の概要からお聞かせください。
藤森氏(以下、敬称略) 当社は食品、改良剤、ヘルスケアの3事業を核として、海外では改良剤事業を主に展開しています。食品事業ではドレッシングやエキス・調味料、わかめなどが主力商品で、ドレッシングとエキス・調味料関係の生産を担っているのが、1968年に生産を開始した草加工場です。工場の敷地は、約7,200坪であり約320名の従業員が勤務しています。大きな特徴として調味料の開発部門が配置されており、生産部門と密接しながら活動をしていることです。開発と生産は近い距離でものを考えていくという思想が根底にあります。
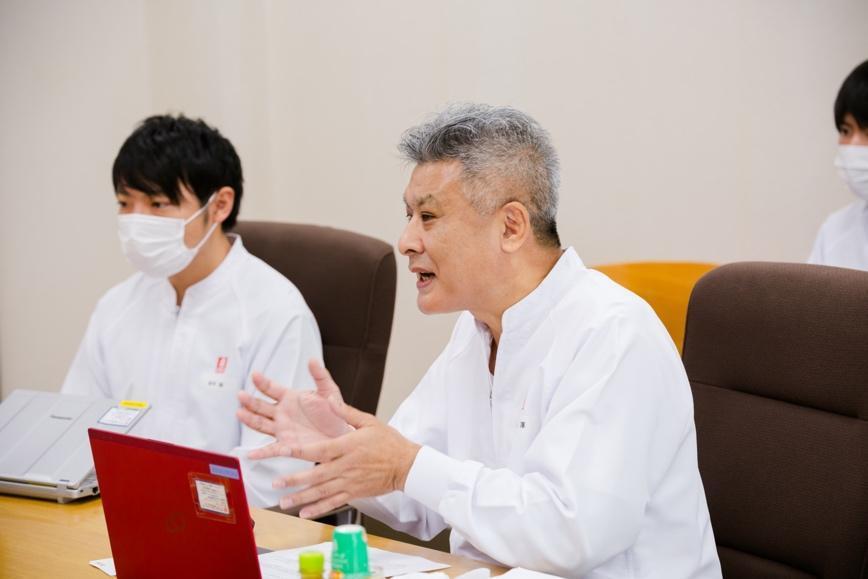
マネジメントシステムにも積極的に取り組み、2000年にISO9001(品質)、2002年にISO14001(環境)、2014年にFSSC2200(食品安全)の認証を取得し、これらを統合したマネジメントシステムとして年1回の外部監査を受け、指摘を受けたところはPDCAを回して改善しています。
田口 製品づくりにおけるこだわりをお教えください。
藤森 当社は天然物の有効利用を基本方針に掲げ、調味料のベースになるエキスをみずから開発し、お客様のご要望に合わせた商品やブランドコンセプトに合致したものづくりをしている点です。たとえば、当社の主力商品である青じそドレッシングやわかめスープには隠し味に独自技術で開発したホタテエキスを有効活用して、差別化やオリジナリティの創出につなげています。
田口 生産を開始してから50年以上過ぎました。課題はありますか。
藤森 少子高齢化に伴う国内市場の縮小や人手不足、原材料・エネルギー費の継続的な高騰など課題は絶えませんが、設備の老朽化は直面する大きな問題の1つとなっています。設備の更新は適宜進めていますが、同時に、安全・品質の担保を行いながら、従業員の人材育成も念頭に置く必要があります。特に、最近では従業員のメンタル面の支援も重要なテーマとなっています。このような事業環境下でどう生産性を向上していくかがポイントとなっており、確りとしたプラットフォームの構築が求められています。
故障した設備のリプレイスがデジタル人材育成の発端
草加工場では省エネや省力化に伴う活動を積極的に推進。これまでに省エネ大賞やIT賞マネジメント部門を受賞し、こうした取り組みがDXにもつながっています。驚きなのは、多くの施策を内製化してきた点です。
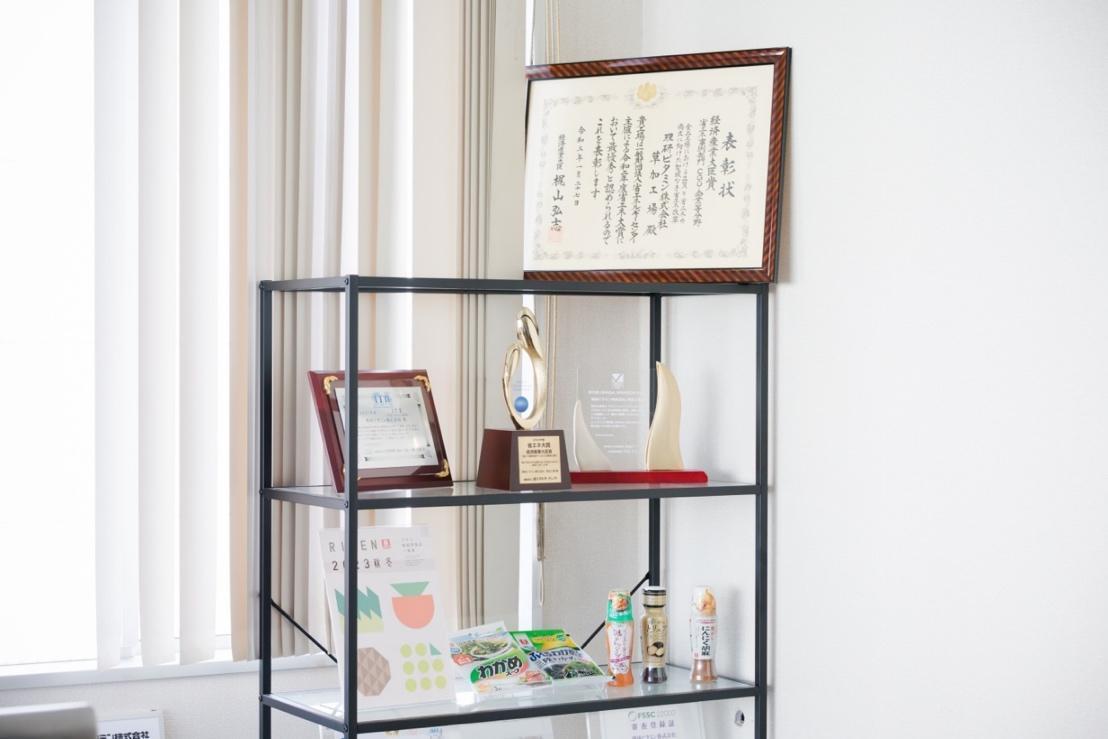
田口 草加工場では省エネや省力化、DXを外部に頼らず、自社内で進めているとお聞きしました。なかなかできることではありません。
藤森 当社は理化学研究所の流れを汲んでおり、企業倫理を守りながらも自由闊達な雰囲気を社風としています。1969年からQC(Quality Control:品質管理)活動を従業員主導で進めるなど、ボトムアップの現場主義が根付いています。こういったDNAは現在も受け継がれ、先輩後輩を問わず課題をみずから解決する文化があり、一連の取り組みを内製化したのは自然な流れでした。ただし、自社で対応しきれない部分は外部にサポートを依頼し、ノウハウの蓄積にも努めています。
田口 DXに取り組み始めた経緯もお聞かせください。
杉浦氏(以下、敬称略) 新規に生産設備を導入する際に、担当者は多くのことを学ぶ機会を得ます。当時の工場長の意向もあって、学んだことを他の従業員にも広げていくことを目的に自主的な勉強会を開催しました。これが切っ掛けとなり若手を集めた各種勉強会が行われました。その後、これらの活動が会社から認められ、2019年にDX化を推進するイノベーション研究会および、その後にBPR研究会が設立されました。
藤森 イノベーション研究会が発足された当時は、DXによる生産性の向上が全社的なテーマとして挙がっていました。このような状況下、草加工場では設備トラブルがこれらの活動に拍車を掛けました。
倉持(以下、敬称略) 生産計画に影響する設備機器のトラブルが発生したため早急に調べた結果、サーボアンプ(サーボモーターの制御機器)が原因だと分かりましたが、制御機器が古くメーカーによる修理対応ができないと連絡がありました。制御機器の入れ替えやプログラムのアップデートには相当な費用が掛かり、且つ、納期まで3ヵ月間待ちという状況でした。その時、杉浦課長から「自分たちでできることはないか」と話を持ち掛けられたのです。
杉浦 生産が終了した制御機器はネットを通して中古品を探しました。また、プログラムに関しても各種検討していくなか、自分たちでも更新できることが分かりました。その結果、低コストで短期間に生産を開始することができたのです。この経験は、その後の我々の活動に大きなインパクトを与えました。まずは、自分たちで草加工場をはじめ国内5ヵ所の工場のアンプを棚卸しすることになりました。翌年には、この活動が大きく評価され、本社の表彰制度で社長賞を受賞するに至りました。
倉持 この社内評価は我々従業員のモチベーションになり、次はPLC(機器・設備などの制御に使われるコントローラー)のアップデートに取り組みました。高額となるPLC更新に関してリスト化して随時作業を実施した結果、相当額のコスト削減に寄与できました。
藤森 この活動も本社で評価され社長賞をいただきました。この一連の経験がデジタル人材の育成の素地につながったことは非常に重要なポイントと考えています。
田口 PLCのアップデートも完全に内製で実施したのですか。
杉浦 メーカーや機器に精通した人に見積もりを依頼したり、プログラムの更新もリスクマネジメントについて外部から学んだりなど、取っ掛かりの学習コストは支払っています。
田口 私はシステムインテグレーターなので内製化をされると立場的に困りますが、現実的には自社で取り組まないと機器・設備を維持できないケースは多々あります。自由闊達な文化がないと内製化にはたどり着かなかったのではないでしょうか。
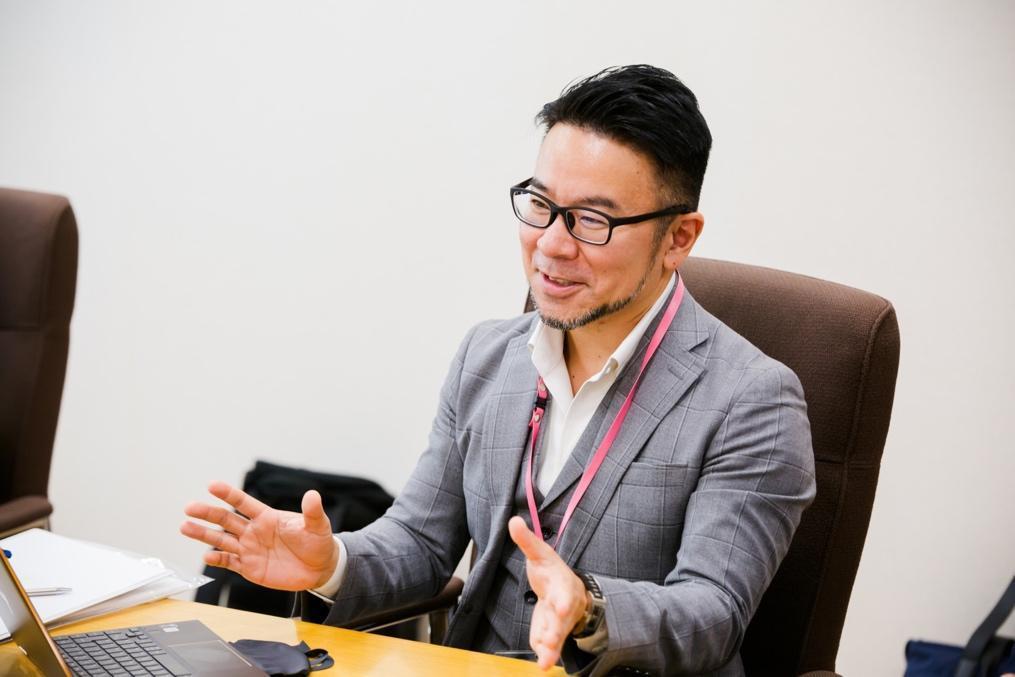
ビッグデータを収集して在庫管理・メンテナンスに活用
工場見学の一場面。導入から約20年経ったコンテナ洗浄機のPLCのアップデートについて解説する倉持氏。タッチパネルの生産はすでに終了しており、自社でリプレイスを計画・実行。その後もイーサネット機能を追加し資材管理に活用するなど、新たな動きも見られています。異常が発生すると音声で知らせるなど、機能の拡張も行っています。
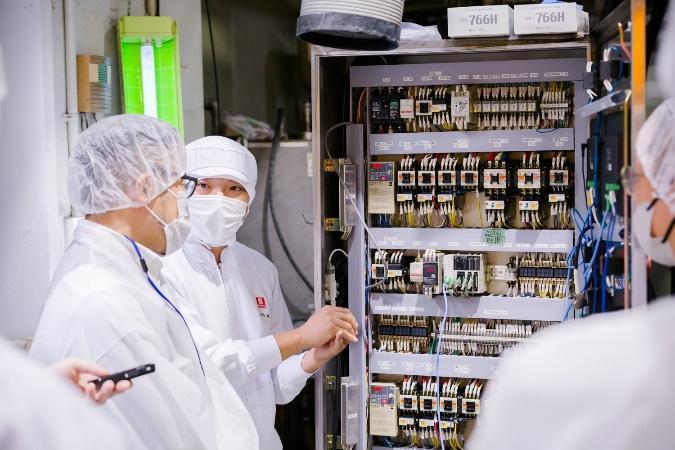
田口 自主的な勉強会と製造機器のトラブルがDXにも波及していったのでしょうか。
藤森 機器のアップデートに関わったメンバーがイノベーション研究会に参加したことで、具体的な取り組みが加速していきました。
杉浦 若い従業員にはスマホと製造機器をつなげてリモートで監視するなど、さらに手を伸ばす必要性を説きました。実際に多くのメンバーはDXに関心があり、プログラミングに関しても一から考えるのではなくネット情報も参考にするなど、みずから学びながら取り組みを広げています。
倉持 サーボアンプとPLCのリプレイスで微弱電流の基礎知識を学び、制御関連の技術者が育ちました。また、イノベーション研究会が発足したことで、DXに興味を持つ若手に実務の機会が生まれたことも大きいです。
会社に成果を認められたことで活動自体がさらに活性化しました。具体的には、これまでモニタリングしていても使われなかった情報を見直して分析後に有効活用する動きです。PLCにイーサネット機能を追加してPCとつなげ、エクセル上でデータ管理を行い、資材課にて在庫調整に有効活用する仕組みを実現しました。
また、主要設備機器のサーボモーターにかかる負荷の情報なども今までは有効活用できていませんでした。実際は、ベアリング部分に製品由来の粉末などが侵入するとベアリング機能が低下して滑りが悪くなりトルク値が上昇します。そこに注目し、PLCからサーボモーターのトルクを常時監視し、閾値を超えたらメンテナンスする取り組みを開始しました。
熊本氏(以下、敬称略) サーボモーターの情報をPCのエクセルファイルに情報を自動で取り込み、クラウド型ツールに転送してトルク値をグラフ化しています。
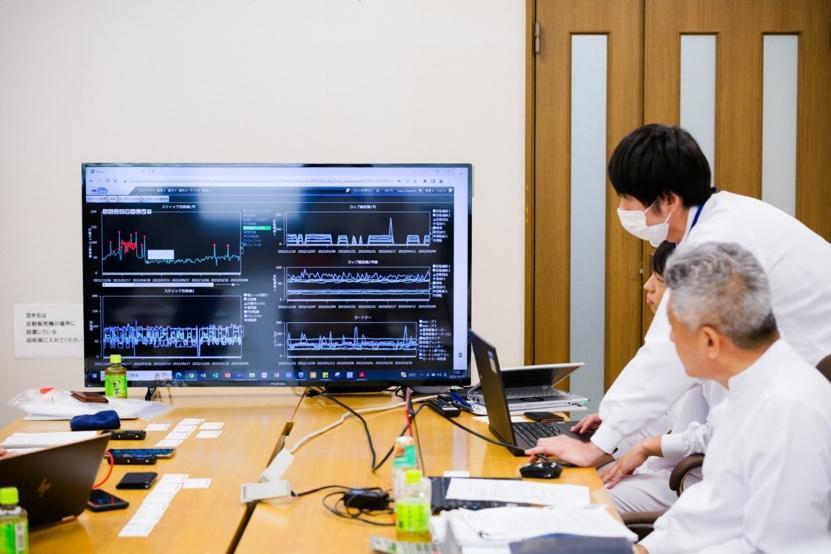
熊本 ピーク値を頻繁に越えるサーボモーターが確認できたら、その都度部品を交換します。同時に、データから突発的にピーク値を越えた原因も併せて解析しています。機器の組み立て方が上手くいっていなかったなど理由を明確化することを心掛けています。
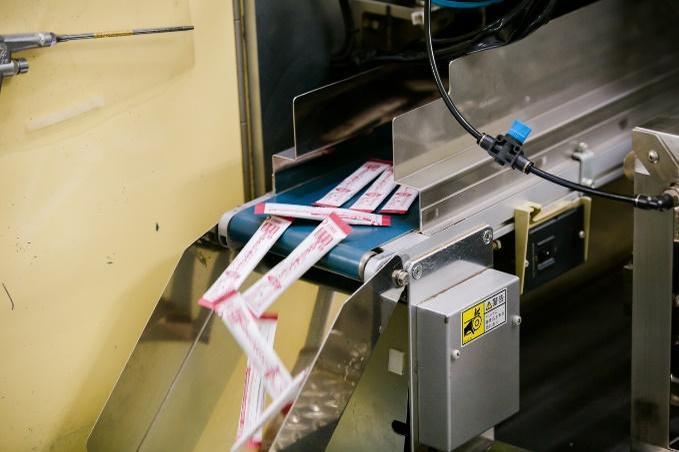
工場見学の一場面。素材力だしの梱包機では、計量装置に使われているサーボモーターのトルク値を遠隔で監視。メンテナンスの最適化を実現しています。
倉持 機器が突然に停止すると半日がかりで復旧することになり、生産に大きく影響してしまいます。
杉浦 また、このような微細な状態変化に気付かずに運転し続けると他の部品に影響を与え高額な修理につながってしまいます。このような活動は品質不良の防止効果もあります。
熊本 今までは稼働率や生産量に関係なく決まった時期に定期的にメンテナンスしていましたが、主要機器の運転状況を常に監視し、そこから発生する異常値から適宜メンテナンスをする方式に切り替えるようになりました。
田口 本来は外部に任せられる作業を自社で行う文化があるのは、製造業として強みになりますね。
間接部門では業務効率化・ペーパーレス化に向けアプリを自作
藤森 製造部門だけではなく事務所での合理化も必要となります。2021年にBPR研究会はそのミッションを持って発足されました。
井上氏(以下、敬称略) 私が所属する生産技術課がBPR研究会の事務局で、全体的な構想を練っております。まずはペーパーレス化、さらに業務管理サービス「Kintone(キントーン)」で業務アプリを自作する取り組みを進めてきました。
田口 アプリの自作とは驚きです。
石川氏(以下、敬称略) 現時点で約300個以上のアプリを作ってきました。具体例として稟議書のペーパーレス化があります。丁度、コロナ禍で在宅勤務制度を導入していたのでタイムリーなテーマでした。この活動によって意思決定のスピードが向上し、ペーパーレス化にも貢献できました。国内他工場にも水平展開しています。
田口 アプリ制作はスムーズに進みましたか。
石川 アプリ制作より社内に浸透させるのに苦労しました。簡単に分かり易く説明すること、使用方法を繰り返し丁寧に説明することを心掛けました。
現在は予算から発注、納品、請求書処理などの情報をつなげる開発も進めています。さらに今後は、生産部門と事務所をシームレスに結び付けるシステムの構築が求められてきます。一方で、相性が良くなかったアプリは整理していかなくてはなりません。
田口 日々の業務と並行して個人がここまでできるのは、非常に素晴らしいことです。
藤森 自分たちで苦労して工程改善を行い、その結果をみずから体験していく、このサイクルが良い効果を生んでいるのかも知れません。これらの活動を上司がQCテーマに落とし込み、成果を“見える化”していることも重要な点となります。
田口 多くの企業はリスク回避のため、内製化を許可しません。御社は自由闊達と言いますが、アクションにつながる環境があること自体が大きなポイントですね。
藤森 リスクは常に念頭に置いて進めてもらっています。専門家のアドバイスを仰ぎながら自分たちの領域を決めて活動するのが基本となります。
人材育成や組織改革が今後の課題
田口 多くの取り組みの中から事例をご紹介いただきました。ありがとうございます。1つ気になるのは、メイン業務と並行して行うとなると人事評価が難しいのではないでしょうか。
藤森 当社では年2回、具体的なテーマとゴールおよび、その施策を上司と協議して設定する目標面接制度があります。このシステムが人事評価と連動しています。このシステムに、メイン業務に加えてこれらのDX活動も取り入れてもらい、直属の上司にも積極的に支援してもらっています。また、DX活動そのものが、自主的な側面があることから、締め付け過ぎず、心理的安全性を醸成させながら進めることが大切と考えています。
田口 さらなるDXの深化に向け、皆さんから一言ずつお願いします。
倉持 工場内ではDX活動にまだ温度差があるので、引き続き、デジタル人材を増やしていきたいと考えています。そのためには、確りと活動する機会を作り、かつ、モチベーションを持って取り組んでもらうことが重要と思います。また、活動結果を水平展開してDX活用をさらに進めていきたいと考えています。
熊本 DX活動においては人事異動に伴う担当者の変更も視野に入れて進める必要があります。そのためには、各部署内で具体的に実務ができる人材を増やすことが重要であり、それがDXを浸透させるカギだと思っています。
石川 1㎏の製品を作るための加工費は設定されていますが、生産方法が異なった場合に加工費は当然ながら変化します。今後、生産工程の変更がリアルタイムに加工賃に反映されるシステムについても考慮していきたいと考えています。このようなシステムが構築できれば生産計画や在庫に対する視点も変わってくる可能性があります。今の活動をさらに活性化してDXの本質に迫りたいと思っています。
井上 IT賞を受賞するなかでデータを収集する基盤は構築できました。ただし、活用に関してはこれからのテーマであり、生産性を向上させるために製造部門と事務部門がどれだけ貢献しているか“見える化”できる仕組み作りも必要と考えています。多様な切り口で評価できる仕組について考えていきたいと思います。
杉浦 これからはデータアナリストを育成していく必要があります。DXの第一段階までは内製化できましたが、取得したデータを活用するためには分析スキルを持つ人材が必要であり、次の段階に向かって進む必要があります。
藤森 我々は基本的に3年単位で活動しており、現在は第9次中期経営計画の途中となります。2025年度から始まる新たな中期経営計画に向け、確りとしたプラットフォームを作り上げる必要がありますが、何より人材育成が重要です。みずから学んで仕事に活かし、成果が出れば評価に結び付け、次の活動に進めていくといったサイクルを回すことが大切なポイントです。
現在、イノベーション研究会および、BPR研究会がありますが、これから先、継続的に活動を活性化していくためには、マネジメント・リーダーシップ的な要素も求められてきます。このような視点は忘れてはなりません。また、DX活動の大きな目的として生産性の向上がありますが、あくまでもお客様あっての活動になります。最終的にこの活動をお客様とどのように結びつけるかも視点に入れ、今後も様々な取り組みを積極的に進めていきたいと考えています。
田口 CCTはスマートファクトリーなどが得意な領域で、お客様と伴走しながら取り組みを進め、最終的には内製化した形でバトンをお渡ししています。そこで思うのは、優秀な人材は社内だけではなく社外にもいるので、一時的に頼って効率的にプロジェクトを進める方法もあるということです。IT関連には外部に優秀なフリーランスもいるので、基本的には御社が主導する形で活用すると、よりパワフルにDXが進むはずです。そういった形で内製化を成し遂げていただきたいですね。本日はありがとうございました。
編集後記
食品の量産は単位時間当たりの生産量や無駄を増やさないなど、生産性自体が極めて重要です。生産性を追求するのに設備メーカーはそこまで面倒を見ませんから、自社でメンテナンスまでできる環境を持つことはとても意味があり効果も見いだせます。量産系の設備は停止すると時間当たりの損害額が計算できるからこそ、怖くて手が出せません。ところが、理研ビタミンではむしろ積極的に取り組んで効率化を実現しています。心理的安全性が確立しているからでしょうし、上司が部下を守る様子がイメージできます。現場が委縮しないで動けるのは大切で、評価システムも含めて働き方がデザインされているのが、最大のポイントです。
【関連リンク】
理研ビタミン株式会社 https://www.rikenvitamin.jp/
株式会社コアコンセプト・テクノロジー https://www.cct-inc.co.jp/
【こんな記事も読まれています】
・【会員限定動画】サプライウェブで実現するマスカスタマイゼーション時代の企業戦略
・製造業における購買・調達業務とは?課題の解決方法も紹介
・ビジネスや技術のトレンドに反応しながら進化を続けるCRMの事例を紹介