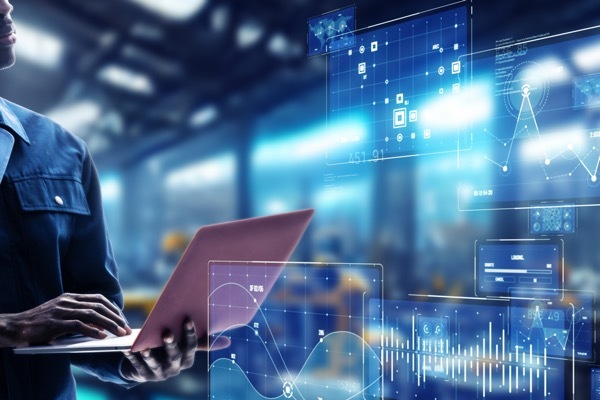
本記事は、木村哲也氏の著書『Small Factory 4.0 第四次「町工場」革命を目指せ! ― IoT の活用により、たった 3年で「未来のファクトリー」となった 町工場の構想と実践のすべて』=株式会社三恵社、2018年8月1日発行の中から一部を抜粋・編集しています。
(1)「できる目標ではなく必要な目標」
たとえば当社では、第1章で述べた技術を用い、「製造ライン遠隔モニタリングシステム」を完成させ、サービスを開始しました。 このシステムは生産数や停止時間など現場で必要な情報をリアルタイムに自動検出・「みえる化」するもので、「サイクルタイムモニター」と「i スマートあんどん」を統合した機能を果たします。
私たちはこのシステムを、「負荷の高いラインの時間当たり出来高を向上させ、休日出勤や残業をなくす。また、追加の設備投資を抑える」という目標のために使っています。
しかし、ここまではどこの企業でも大小の違いはあれ行っていることです。
当社の特色は、この目標設定にあります。
私たちは、目標設定を「できるかどうか」ではなく「必要か否か」で判断します。
つまりこの場合、「休日出勤や残業をなくす」ために時間当たり出来 高 180 個が必要だと算出されたとすると、それが現在の実績に比較して実現可能性の低い数字であっても、目標を修正したりしません。当社も以前は「必要か否か」ではなく「できるかどうか」で目標を設定していました。しかしそれではなかなか新しい知恵が出てこないこと がわかったのです。
「必要な目標」を掲げて「達成するまで知恵を出し続ける」
生産設備のIoT 化は、このための強力な支援ツールなのです。
(2)ほめて、活動の活性化を促す
このシステムを用いると、製造ラインの良い点と悪い点が細かな部分 まで把握できます。だからといって、経営者や責任者が悪い点ばかりを指摘し、「改善しろ、努力が足りない」と現場の尻を叩くと、逆に改善 活動が停滞してしまうことが往々にしてあります。
経営者や責任者は「ほめましょう」。
まずは良い点に注目してあげるのです。
一番簡単なのは「サイクルタイム」のチェックです。
図 2.1 の左側のCTが設定されているサイクルタイム、右側のAVG. CTが停止に至らない実際のサイクルタイムです。0.5 秒短縮されていることがわかります。
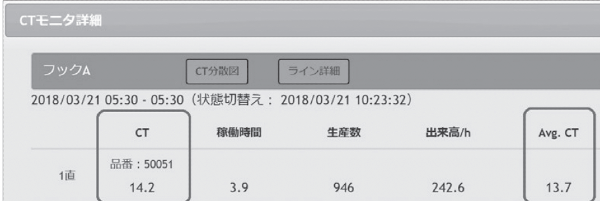
データを確認する際は、まずここに着目してください。そして短くなっているサイクルタイムを発見したら、すぐに現場へ行って「何を改善したの?」と尋ねてください。一度や二度では効果があがりません。これを繰り返しましょう。
すると現場のほうは、「そろそろ社長が来るんじゃないか」と待ってくれるようになります。そして改善点を嬉々として説明してくれるでしょう。さらに「なるほど! よくやった! ありがとう!」とほめてあげれば、現場はさらに知恵を絞ってくれます。
このように、経営者や責任者がきちんとデータを見てそのことを現場に伝えることはとても重要です。私の経験からも、部長や課長が頻繁に足を運び、現場をほめるラインは、驚くほど改善が進みます。
(3)足跡を残せ
現場では、経営者や管理者が社員と直接コミュニケーションをとるのが一番です。最低でも現場に足跡を残すようにしましょう。「上司が来ている」と意識するだけで、大いに刺激に与えることができるからです。また、足跡が残っていれば、その場にいなかった社員に も来たことがわかります。
私はそのために、次頁写真 2.1 のスタンプのセットを買いました。「たいへんよくできました」「よくできました」「ふつうです」「もうすこしです」「もうすこしがんばりましょう」がありますが、(2) で述べたように「ほめる」だけなので、「たいへんよくできました」と「よくできました」しか使いません。スタンプを捺す対象はなんでもありです。 安全のボードだったり、改善結果だったり。「いいね!」と思ったらペタリ、です。
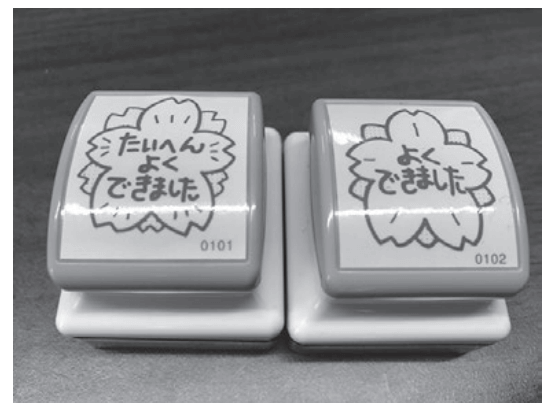
(4)コメントを残す
(3) をさらに進めてみましょう。
以下は当社の西尾工場の例です。
現場に改善後と改善前のサイクルタイムのばらつきを示すヒストグラ ムが貼り出されていました。平均が 25.4 秒から 24.4 秒に向上しているとともに、ばらつきが小さくなっていました。改善活動に積極的に取り組んでいる証拠です。私はそのヒストグラムに「よくできました」のスタンプを捺しました(写真 2.2)。
しかしそれだけでなく、ヒストグラムの右下に「標準偏差を計算してみてSTDEV木村」とサインをしました。
「STDEV」とは、標準偏差を計算するエクセルの関数です。標準偏差が小さければデータ分布のばらつきが小さいという証です。
さて、私がコメントを書いてしばらくすると、件のヒストグラムに「標準偏差 1.8」「標準偏差 1.3」と書き足してありました。現場の誰かが、さっそく計算してくれたに違いありません。話すだけがコミュニケーション ではありません。ちょっとしたコメントをやりとりするだけで、心を通じ合わせることも、何かを教え合うこともできるのです。
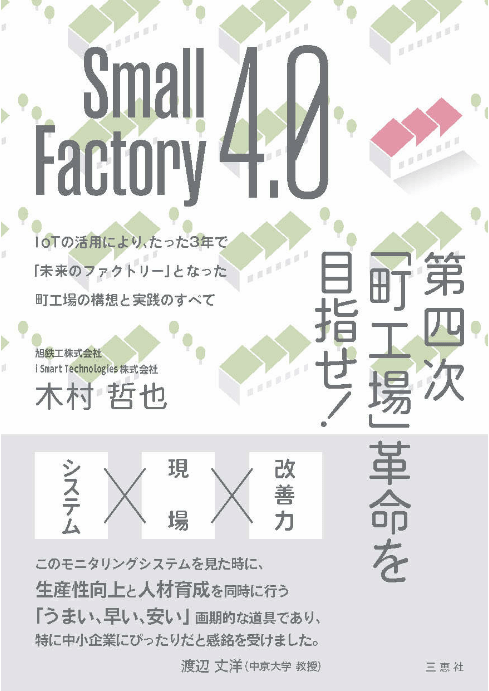
1992 年東京大学大学院工学系修士修了、トヨタ自動車㈱に21 年勤務。 主に車両運動性能の先行開発・製品開発に従事。また、生産調査部でトヨタ生産方式を学び内製工場および社外の指導を経験した。
2013 年に旭鉄工㈱に転籍、生産調査部での経験を生かし、生産性・組織や仕事の進め方など経営全般を大きく改革。その中で製造ライン遠隔モニタリングシステムを構築・運用、生産性向上と人材育成の面で大きな成果をあげる。 他の中小製造業でも同様に生産性向上を実現するため、このシステムをサービスとして提供する「i Smart Technologies ㈱」を設立した。
現在、本システムは中小企業を中心に100 社以上に導入され、「第7回 ものづくり日本大賞 特別賞」をはじめ数多くの賞を受賞した。また2018 年にはその実績が認められ、タイ王国工業省とシステム導入・発展に関する「覚書」を締結した。
※画像をクリックするとAmazonに飛びます
【こんな記事も読まれています】
・【会員限定動画】サプライウェブで実現するマスカスタマイゼーション時代の企業戦略
・製造業における購買・調達業務とは?課題の解決方法も紹介
・ビジネスや技術のトレンドに反応しながら進化を続けるCRMの事例を紹介